When finding brown spots on the surface of Stainless steel casting, people are very surprised, thinking that "stainless steel will not get rusty. This must not be stainless steel. There must be a problem with the steel." In fact, this is a one-sided view resulting from a lack of understanding of stainless steel. Stainless steel will also rust under certain conditions.
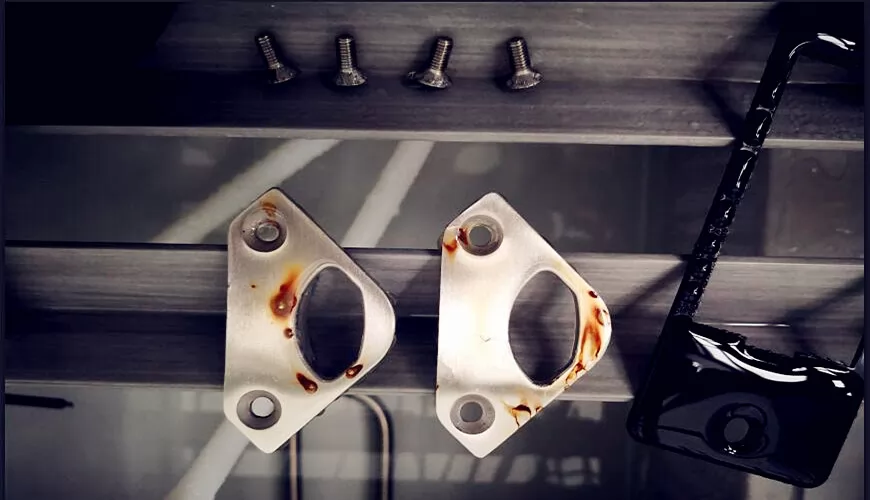
Stainless steel has the ability to resist atmospheric oxidation-that is, corrosion resistance. Stainless steel relies on an extremely thin, strong, dense and stable chromium-rich oxide film (protective film) formed on its surface to prevent the infiltration and oxidation of oxygen atoms, thereby obtaining the ability to resist rust. However, the size of its resistance to modification varies with the chemical composition of the steel itself, the processing state, the conditions of use, and the type of environmental medium. Once for some reason, the oxide film on the surface of the stainless steel is destroyed, the oxygen atoms in the air or liquid will continue to infiltrate, or the iron atoms in the metal will continue to precipitate ions to form loose iron oxide, and the metal surface will be under continuously corrosion. Taking 304 steel as an example, it has excellent corrosion resistance in a dry and clean atmosphere, but when it is moved to the seaside area and placed in a sea fog which contains a lot of salt, it quickly rusts. However, when it comes to 316 steel, it performs well in this situation. Therefore, there is no kind of stainless steel resistant to corrosion and rust in any environment.
1.1 Surface pollution: Oil dirt, dust, acid, alkali, salt, etc. attached to the surface of the workpiece are converted into a corrosive medium under certain conditions, and they react chemically with certain components in the stainless steel parts, resulting in chemical corrosion and rust.
1.2 Surface scratches: Various scratches damage the passivation film, which reduces the corrosion resistance of stainless steel, and easily reacts with chemical media, resulting in chemical corrosion and rust.
1.3 Cleaning: After pickling and passivation, the cleaning is not removed thoroughly, resulting in residual liquid, which directly corrodes the stainless steel parts. For example, during pickling, the acid liquid enters the shrinkage cavity of the casting (as shown below), and then reacts with the air to cause yellow spots on the surface of the casting.
Such yellow rust spots often do not appear immediately, so it is difficult for the factory to detect them. When the yellow rust spots appear on the surface of the casting after a period of time, the product may have reached customers, causing trouble to them. The advantage of Besser Casting is to optimize the internal process to avoid shrinkage cavity of the casting, so as to avoid the acid liquid from entering the shrinkage cavity after pickling.
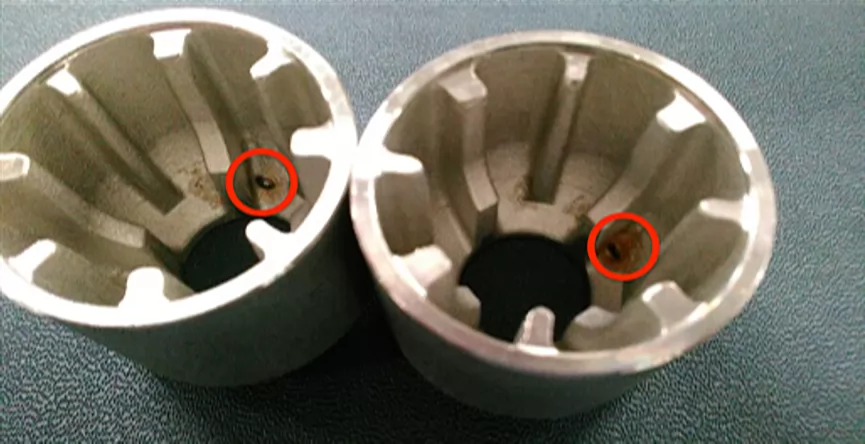
2.1 Carbon steel pollution: Scratches caused by contact with carbon steel parts and corrosive media form galvanic cells and produce electrochemical corrosion.
The carbon steel pollution of stainless steel castings generally comes from the shot blasting process in the casting production process. The shot blasting process is to use countless small steel shots to hit the product with great force, so as to clean the sand on the surface of the product. Generally, foundries will use carbon steel shots, which have a chance to adhere to the surface of stainless steel, resulting in rust spots on the surface of castings. That’s why casting products will rust after they reach customers for a period of time.
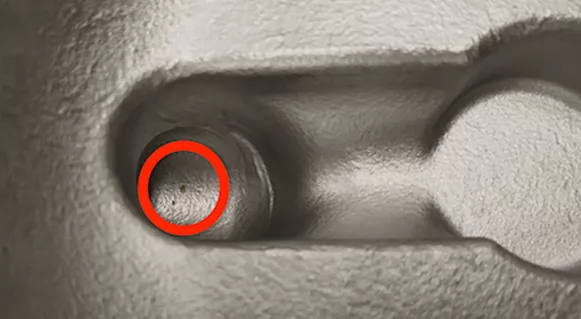
2.2 Cutting: Adhesion of rusty materials such as slag and splash and the corrosive medium form a galvanic cell and cause electrochemical corrosion.
2.3 Heating: The composition and metal structure of the flame heating area change unevenly, forming a galvanic cell with a corrosive medium and causing electrochemical corrosion.
2.4 Welding: Physical defects (undercuts, pores, cracks, unmelted, not fully penetrated, etc.) or chemical defects (coarse grains, chromium-depleted grain boundaries, segregation, etc.) of the welding parts form a galvanic cell with corrosive medium and cause electrochemistry corrosion.
2.5 Material: Chemical defects of stainless steel (uneven composition, S, P impurities, etc.) and surface physical defects (loose, trachoma, cracks, etc.) of workpieces form a galvanic cell with corrosive media and cause electrochemical corrosion.
2.6 Passivation: The passivation effect of pickling is not good, resulting in uneven or thin passivation film on the surface of stainless steel, which is prone to electrochemical corrosion.
2.7 Cleaning: The remaining acid-washing passivation residual liquid chemically corrodes the product of stainless steel and causes the electrochemical corrosion of the stainless steel parts.
In short, due to its special metal structure and surface oxide film, stainless steel is generally difficult to be corroded by chemically reacting with the medium, but it does not mean that stainless steel cannot be corroded under any conditions. The corrosion mechanism of stainless steel parts is mainly electrochemical corrosion. In the presence of corrosive media and incentives (such as scratches, splashes, slag cutting, etc.), stainless steel will corrode slowly chemically or electrochemically with corrosive media. What’s more, under certain conditions, the corrosion rate is quite fast and rust occurs, especially in form of pitting and crevice corrosion.

Therefore, all effective measures should be taken during the processing of stainless steel products to avoid the occurrence of corrosion conditions and incentives. In fact, many rusting media and incentives also have a significant adverse effect on the appearance quality of the product, and thereby should and must be overcome. Besser Casting can provide you with professional surface treatment services to prevent stainless steel castings from rusting through blackening, phosphating, pickling and passivation. If you want to know more about surface treatment or have certain requirements, please contact us by any means.