Lost wax casting, also known as "investment casting", is a traditional technique from ancient China, which has been further improved with the help of modern technology. This guide will introduce you to this wonderful magic from the ancient East in a simple and easy-to-understand way.
Define Lost Wax Casting
Lost wax casting, also known as the lost wax method or lost wax investment casting, is a production technique that originated in ancient China. This method involves creating a detailed wax model, which is then encased in a ceramic shell. Once the wax is melted away, molten metal is poured into the mold, resulting in a highly detailed metal object. Despite its ancient origins, this technique remains one of the most effective ways to capture intricate details in metal products today.
Lost Wax Casting Examples
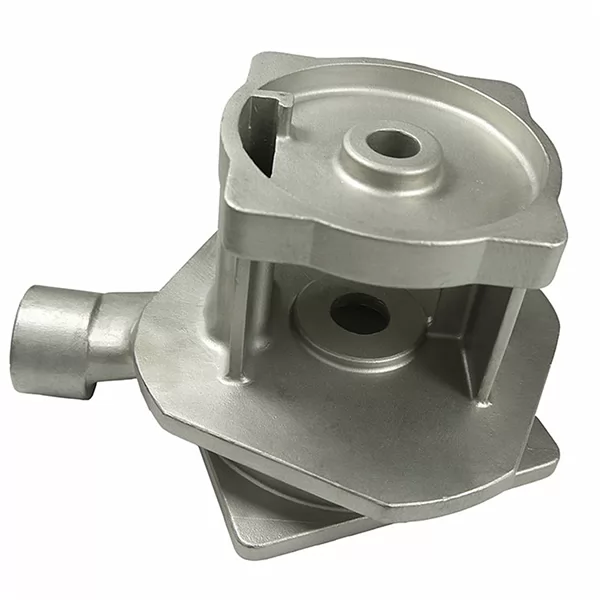
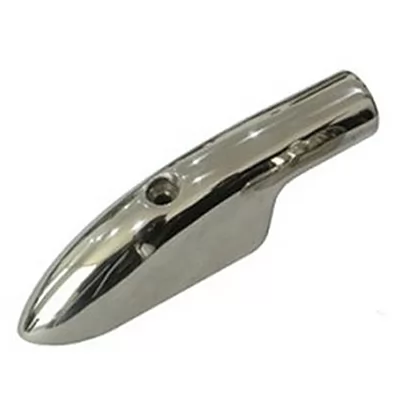
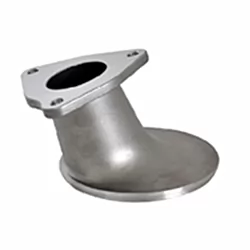
What Is the Lost Wax Casting Process?
The lost-wax casting process can differ depending on the industry and application, but it generally consists of the following steps. Cast parts can be made from a wax model itself, called the direct method, or from replicas of the original wax model, called the indirect method. The direct method jumps from step one straight to step four.
Step 1: Model-making
The engineer carves a design out of wax. The size and complexity of the wax model is limited to the wax carver’s skill, and the capacity of his casting equipment.
Step 2: Creating a mold
A caster then casts this model and polishes the casting to produce a “master” pattern. The master model is used to make a wax mold out of rubber, which is heated and “vulcanized” around the master casting to make a flexible wax mold.
Step 3: Producing wax patterns
Molten wax is injected or sometimes poured into the rubber mold. This can be done over and over to make copies of the original design.
Step 4: Assembling the wax pattern
Sprues are added to the wax copies and they’re connected to create a tree-like structure, which provides paths for the molten wax to flow out and molten metal to later fill the cavity.
Step 5: Applying investment materials
The wax tree is either dipped into a slurry of silica, or put into a flask and surrounded by the liquid investment plaster.
Step 6: Burnout
After the investment material dries, the flask is placed upside down into a kiln, which melts the wax leaving a negative cavity in the shape of the original model.
Step 7: Pouring
The investment mold is further heated in a kiln to reduce the temperature difference with the molten metal. Metal is melted and then poured, using gravity or vacuum pressure to pull the metal into the cavity.
Step 8: Devesting
Once the molten metal has cooled somewhat, the investment mold is quenched in water to dissolve the refractory plaster and release the rough casting. . The sprues are cut off and recycled, while the casted parts are cleaned up to remove signs of the casting process.
Step 9: Finishing
The casted parts are filed, ground, machined, or sandblasted to achieve final geometry and surface finish. Where necessary, the cast parts are also heat-treated to enhance the mechanical properties of the material.
What Are the Best Materials for Lost Wax Casting?
One of the reasons lost wax casting is so popular is that there is no limit to the number of metals that can be applied to the process. We recommend the most common types of metal materials for you.
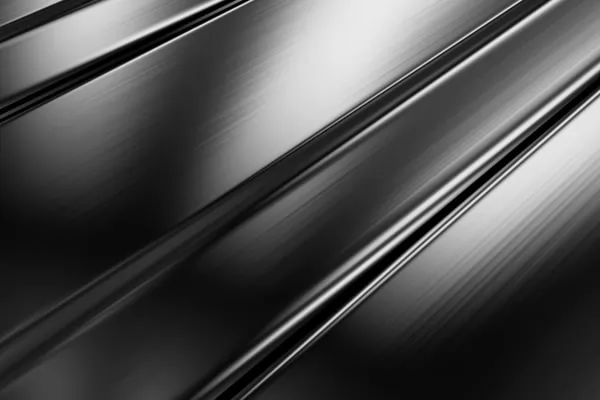
Stainless steel
The main alloys of stainless steel are chromium, nickel and molybdenum, which determine the grain and mechanical properties of the casting. The way the alloys are combined determines the heat and corrosion resistance of the casting.
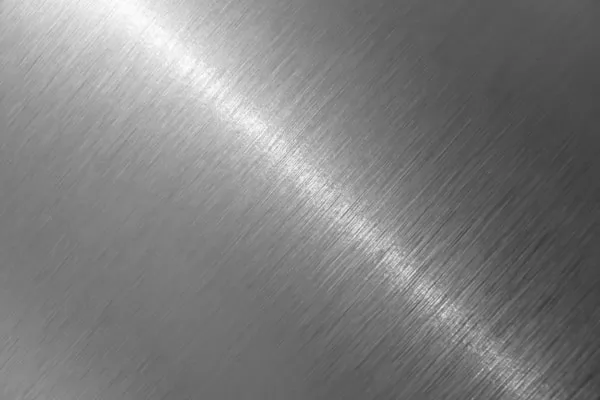
Steel
Carbon, low alloy and tool steels are used in the aerospace, agricultural, medical and firearms industries, to name a few. Steel is chosen for lost wax casting because it is economical, available in a variety of grades, and its ductility can be adjusted through heat treatment.
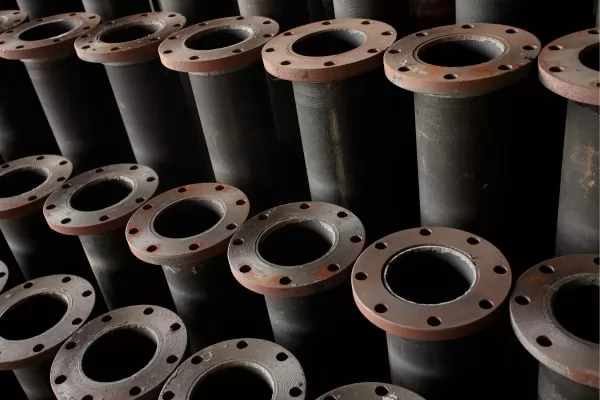
Ductile Iron
Ductile iron castings have excellent surface hardness, modulus of elasticity, corrosion resistance and a strong strength-to-weight ratio. The biggest benefits of ductile iron are that it is cost-effective and offers a wide range of design freedom.
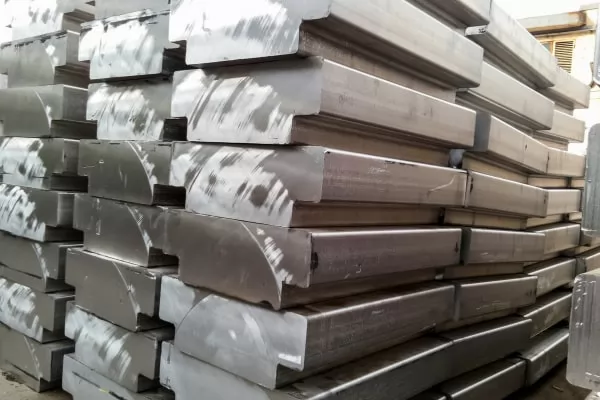
Aluminum
Aluminum is the ideal metal for lost wax casting due to its machinability and corrosion resistance. When it is alloyed with other metals and heat-treated, it develops extraordinary strength that rivals that of mild steel.
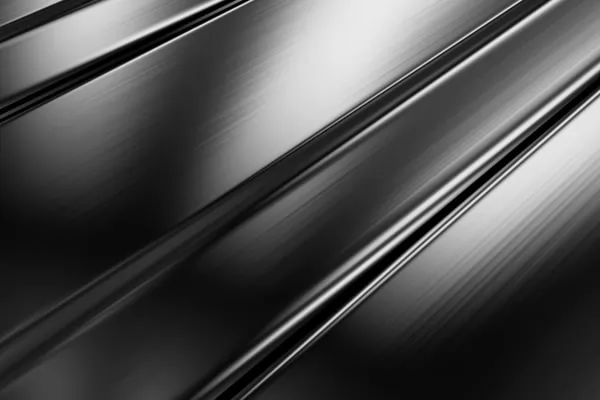
Cobalt
Cobalt is naturally resistant to oxidation and has a hard and shiny surface. It prevents oxidation by passivating the oxide film. Cobalt's resistance to corrosion, heat and wear makes it ideal for lost-wax casting and is used to produce parts for the aerospace, automotive industry and military applications.
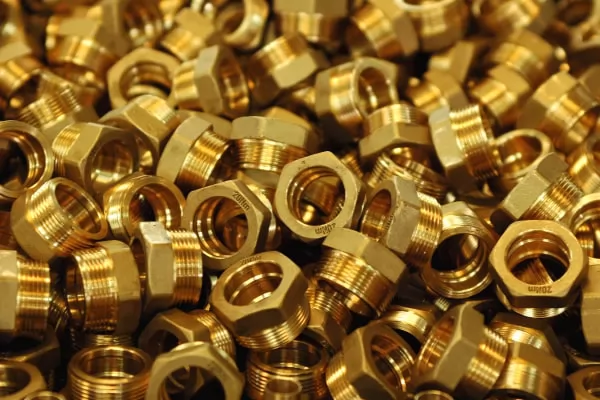
Brass
Brass is a copper alloy known as red brass or brass, and the lost-wax casting is used for plumbing fixtures and door hardware. The main characteristics of brass are its appearance and quality of finishing and polishing. One disadvantage of using brass is its lead content, which limits its use.
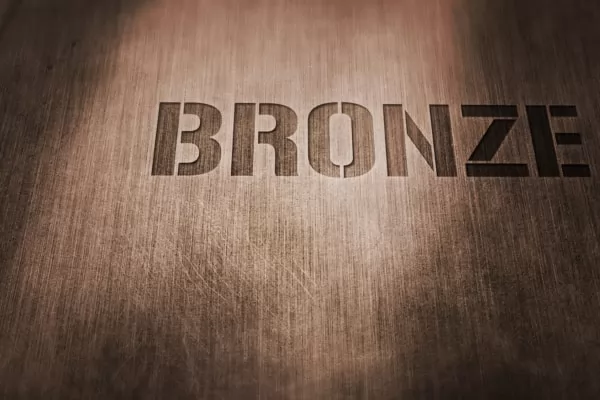
Bronze
The properties and quality of bronze depend on the alloy it is combined with. Added elements to bronze can enhance its performance and quality.
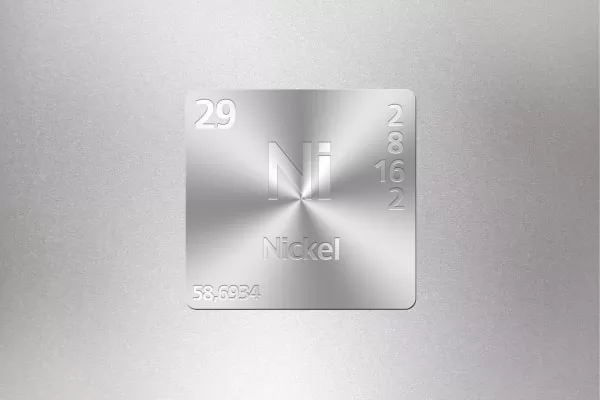
Nickel
Nickel, containing nickel, chromium and molybdenum, has exceptional strength and resistance to heat, wear and corrosion. It was chosen as the cast metal because it is easy to weld and fabricate, and it is resistant to cracking and corrosion.
What Are the Main Applications of Lost Wax Casting?
Automotive Parts
Lost wax casting is extensively used in the automotive industry to produce a wide range of precision parts. Components such as engine blocks, transmission cases, and intricate brackets are often made using this method due to its ability to create complex shapes with high accuracy. The process ensures that parts are durable, resistant to wear, and able to withstand the demanding conditions of automotive applications.
Construction Hardware Casting
In the construction industry, lost wax casting is employed to manufacture various hardware components, including hinges, locks, and structural connectors. The method allows for the production of parts with fine details and strong mechanical properties, which are essential for the safety and integrity of construction projects. The flexibility of lost wax casting also enables the creation of custom-designed parts tailored to specific architectural needs.
Bathroom Hardware Casting
Bathroom fixtures and hardware, such as faucets, showerheads, and towel racks, are often produced using lost wax casting. This process allows manufacturers to create products with intricate designs and smooth finishes, which are not only aesthetically pleasing but also highly functional. The corrosion resistance and durability of the casted materials make them ideal for use in the moist environment of bathrooms.
Agricultural Equipment Casting
Bathroom fixtures and hardware, such as faucets, showerheads, and towel racks, are often produced using lost wax casting. This process allows manufacturers to create products with intricate designs and smooth finishes, which are not only aesthetically pleasing but also highly functional. The corrosion resistance and durability of the casted materials make them ideal for use in the moist environment of bathrooms.
Hydraulic Equipment Casting
Hydraulic systems rely on precise, robust components to function effectively, and lost wax casting is a preferred method for producing these parts. Items such as valves, pumps, and cylinder heads are commonly cast using this technique, ensuring they meet the strict tolerances required for hydraulic applications. The process allows for the production of high-quality parts that can withstand the high pressures and stresses typical of hydraulic systems.
What Is the Difference Between Lost Wax Casting and Forging?
We will use tables to outline some of the content to compare these two different metal processes.
Comparison Dimension | Lost wax | Forging |
---|---|---|
Definition | Casting is a metal-working process where the metal is first heated till it melts, then poured into a mould and made to cool to obtain the shape. | Forging involves the use of localized compressive forces on the solid material in order to create desired shapes. |
Strength | Casted material is low in strength as they are poured into a cavity which lets the material take its shape freely. | Forged material are stronger as they possess a definite grain structure which is pressed with force, increasing their mechanical strength. |
Suitability for Hollow Shapes | Casting is often preferred for the production of material containing hollows spaces or cavities. | Forging excludes cavities and porosity from their compositions. |
Uniformity | The casted material is not always uniform | Forged material can be made to a uniform structure preserving consistency in shape. |
Size Restrictions | Casting doesn’t have any size or shape limitations as all material will be melted before putting them into shape. | Materials weighing up to 50kgs can be forged yet higher power is required if material to be forged is heavier than 50kgs. In this case, casting would be the alternative. |
Level of Complexity | Casting is able to produce complex patterns and shapes. | Forging is more focused in producing uniform and simple material. |
Cost | Casting uses relatively inexpensive equipment. | Machines used for forging such as heavy duty industrial dies are more expensive. |
What Are the Advantages of Lost Wax Casting
1. Precision and Complexity
One of the most significant advantages of lost wax casting is its ability to produce highly complex and detailed parts with excellent precision. This process allows for intricate geometries and fine details that would be difficult or impossible to achieve with other casting methods. The wax model can capture every nuance of the design, resulting in a finished product that closely matches the original specifications.
2. Versatility in Material Choices
Lost wax casting can be used with a wide variety of metals and alloys, including steel, aluminum, bronze, and titanium. This versatility allows manufacturers to select the best material for the application, whether it requires high strength, corrosion resistance, or a specific aesthetic finish.
3. Minimal Waste
The process of lost wax casting is highly efficient, with minimal material waste. The wax models can be reused, and any excess metal from the casting process can often be recycled. This efficiency not only reduces costs but also makes lost wax casting an environmentally friendly option compared to other manufacturing methods.
4. Excellent Surface Finish
Lost wax casting produces parts with a smooth surface finish, often requiring little to no additional machining or finishing. The molds used in this process can capture fine details and create surfaces that are free from defects, reducing the need for further processing and improving the overall quality of the final product.
5. Design Flexibility
Lost wax casting offers considerable flexibility in design, allowing for the production of parts that may combine multiple components into a single piece. This capability can reduce assembly times and costs, as well as improve the structural integrity of the final product by eliminating the need for welds or joints.
6. Dimensional Accuracy
The precision of lost wax casting results in parts with tight tolerances and consistent dimensions. This accuracy is crucial for applications where exact measurements are necessary, such as in aerospace, automotive, and medical industries. The ability to maintain dimensional accuracy across large production runs ensures that each part meets the required specifications.
7. Cost-Effective for Small to Medium Runs
While lost wax casting may have higher initial setup costs compared to some other casting methods, it becomes cost-effective for small to medium production runs. The ability to produce high-quality, detailed parts with minimal post-processing requirements can offset the initial costs, especially when producing parts with complex geometries or specific material properties.
When Is It Appropriate to Use Lost Wax Casting
Complex Geometries: Lost wax casting is capable of producing extremely complex and detailed parts that may contain intricate cavities, thin walls, complex contours, or small decorative features. The process faithfully replicates complex designs without the limitations of traditional casting methods through the use of wax patterns and ceramic shells. It is particularly suitable for fields such as aerospace engine blades, complex mechanical components, and high-precision medical devices.
High Dimensional Accuracy: The lost wax casting process provides excellent dimensional accuracy and tolerance control. Castings typically achieve tolerances of ±0.1mm or finer, which reduces or completely eliminates the need for subsequent machining. Due to this high accuracy, lost wax casting is especially suitable for applications requiring strict dimensional and shape control, such as precision mechanical parts, automotive engine components, and high-performance valves.
Excellent Surface Quality: The process is capable of producing castings with smooth surfaces and rich details, usually without the need for additional surface treatment. This surface finish makes lost wax castings ideal for manufacturing parts with high requirements for surface appearance and feel, such as decorative parts, precision instruments, and medical device components. The smooth surface not only enhances the product's appearance quality but also improves its corrosion resistance and performance.
Medium to Large Batch Production: Despite the high initial mold and tool investment, lost wax casting is cost-effective in medium to large batch production. For orders with production quantities of more than 25 pieces, the reduced post-processing time and labor costs often significantly reduce the overall production cost. The process provides consistent high quality and stability in mass production, making it suitable for fields such as automotive, aerospace, military, and industrial equipment that require high precision and consistency.
What Factors Affect the Cost of Lost Wax Castings?
Let's take a look at some of the cost drivers associated with lost wax casting.
Design Complexity of Castings
Part design is a major factor affecting the cost of lost wax casting. Simple part designs with no internal passages, holes or features help reduce costs for customers.
Material selection
The metal of choice is another cost driver for lost wax casting. There are different grades of common metals and alloys. So even with the same metal, a higher purity alloy will cost more than a lower grade alloy.
Quantity of shell-building layers
As the shapes of investment castings are always different, there will exist differences in shell-building layers. For more complex structures, more shell-building layers will be needed, which will cost more.
Lost Wax Casting FAQs
Q1. How much shrinkage in lost-wax casting?
Q2. What is the maximum size and weight of parts that can be produced using lost wax casting?
Q3. What are the limitations of lost wax casting when it comes to complexity and design?
Q4. How does lost wax casting handle high-performance alloys, and what are the challenges involved?
Q5. What is the typical lead time for producing parts via lost wax casting?
Q6. How does the lost wax casting process accommodate high-production volumes?
Lost Wax Casting Company - Besser Casting
Besser Casting is a leading investment casting company in China. We have more than 20 years of experience in the field of lost wax casting. We have a professional engineering team that oversees and handles the whole process to ensure smooth operation.
In addition, we confirm that all products meet the tolerances specified by ISO standards.
This strict adherence ensures that all of our castings are to exact dimensions.
Our sole purpose is to provide you with quality lost wax casting products at an affordable price.
If you place an order, our professionals will discuss with you the finer details of what you would like to be fulfilled.
Conclusion
Lost wax casting, or investment casting, is a casting process that uses a wax pattern to create the initial design for a part to be produced in a ceramic mold.
Lost wax casting can produce a variety of complex and intricate parts with excellent tolerances.
Lost wax casting is used to produce parts that require tight tolerances with thinner walls and exceptional surface finishes that require very little after process finishing.
The casting process for lost wax casting involves multiple steps that begin with the creation of the pattern, or master, which is made from wax.
Lost wax casting uses a wide assortment of metals to create parts with exceptional accuracy and tolerances.
Lost wax casting is a highly technical process, and with more than 20 years of manufacturing experience, we are able to provide you with lost wax investment casting services. So feel free to inquire about our services and one of our team members will discuss your project needs with you.