Sometimes, a certain supplier may substitute another supplier for a particular part. Generally, this may be a violation of the rules for various reasons: one of them may be shrinkage porosity. In this case, the new supplier must directly develop the product in order to find a better solution.
For example, if the cavity size is large and always in the same position near the gate, it may be necessary to act on different factors, especially the geometry of the runner and gate. Conversely, if the frequency and location of the pores in the casting are different, the expert should study the machine and operating parameters.
For new products, in order to avoid defects, simulation analysis must be performed in the design phase. Simulation is the process of imitating a region using a set of mathematical equations to be implemented in a computer program. The main inputs of the casting simulation process are:
(A) The geometry of the mold cavity (3D model castings, risers and gate channels).
(B) Thermal physical properties (density, specific gravity, thermal and thermal conductivity, and mold material, depending on temperature).
(C) Boundary conditions (ie, mold heat transfer coefficient, applicable to ordinary molds and feed auxiliary equipment, including chilling, heat preservation and exothermic materials).
(D) Process parameters (such as pouring speed, time and temperature).
The use of casting simulation software can eliminate shrinkage porosity, thereby ensuring the flow of liquid metal under high pressure during the solidification phase. Experts should use simulation software to obtain the analysis results of the casting solidification stage.
If the component already exists, the mold must be tested and the casting affected by shrinkage porosity (especially size and defect location) must be analyzed. By strictly considering the shrinkage porosity through casting simulation, the shape and location of the porosity can be identified and the air retention and tracking flow can be predicted.
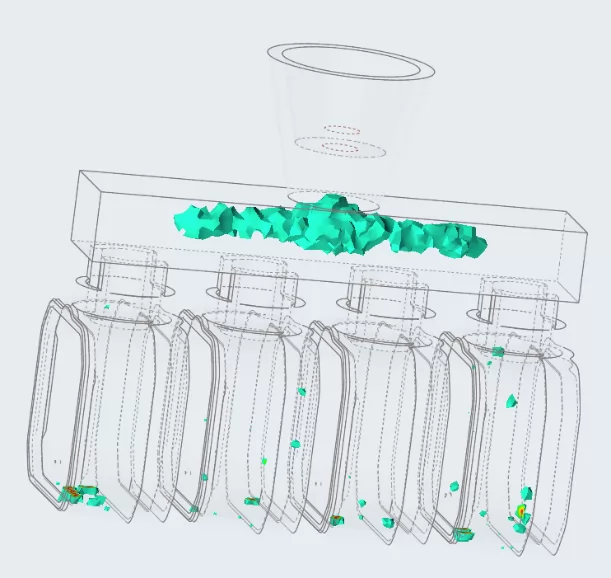
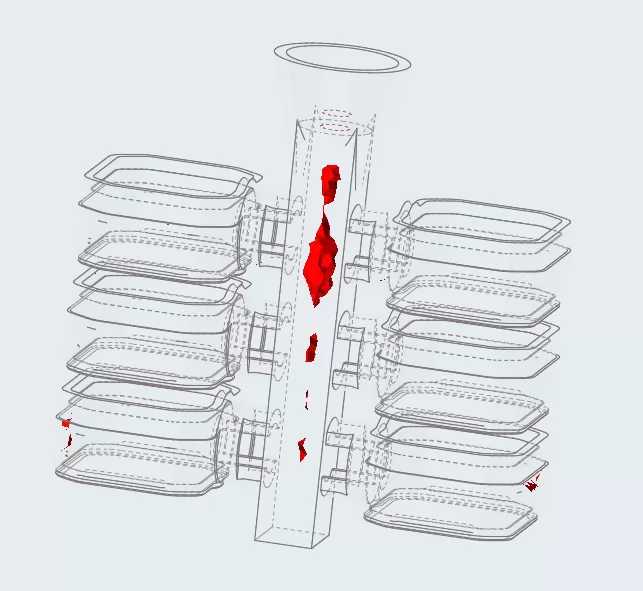
Besser Casting's knowledge in the field of casting simulation ensures a stable process. Determining the appropriate casting configuration during the production process is a relatively complex process, and the results are not always known in advance. Therefore, a computer program is needed to simulate the casting process. The casting simulation is a 3D model that can simulate the entire casting process. Besser Casting has been using the same simulation software for many years and has accumulated a wealth of practical experience and knowledge. Casting simulation provides a high degree of process certainty, prevents technical problems and ensures that the project will not be delayed.
Since Besser Casting has software for performing casting simulations, we can make a significant contribution to the final design and the quality of the casting. We estimate that more than 90% of casting errors are usually caused by design errors, while in fact only 10% are caused by production problems. Many design errors can be found in time by using simulation software. After that, the design or process parameters can be modified. This ensures that no problems arise during the production of castings. The high cost of wrong casting is also prevented. A prototype used to detect errors; now, this is done using a 3D casting simulation. The so-called "trial and error" procedure is now history. This can save a lot of time and money. Using simulation software can well optimize the casting process and castings. It improves quality and greatly reduces production costs.
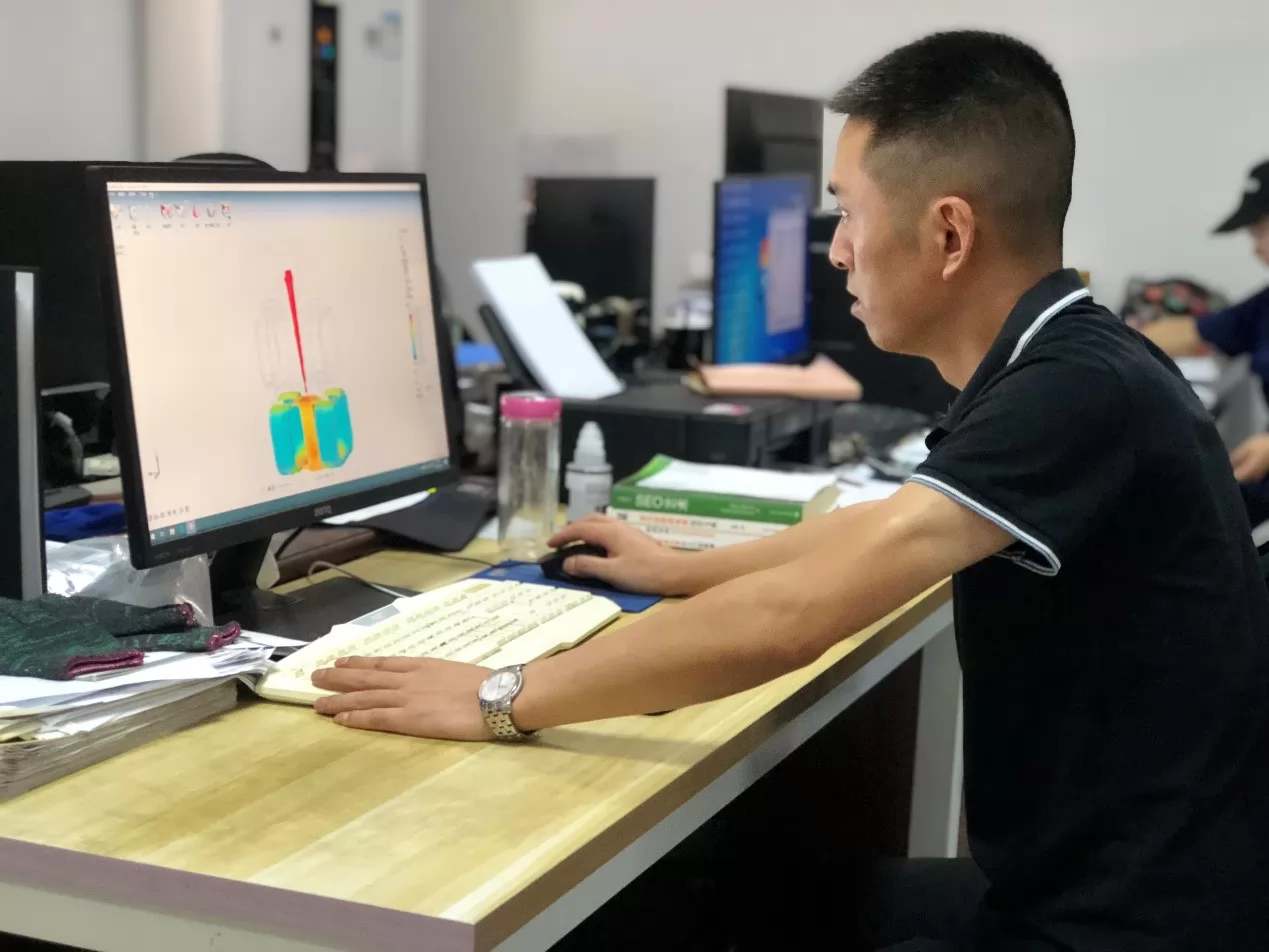
If our engineers can participate in the design process early, our specific knowledge of casting and solidification simulation can bring you huge benefits. Thanks to ESI ("Early Supplier Participation"), the design has been greatly optimized. Therefore, when bidding for castings, don't just choose the lowest price, but also evaluate the quality that can be provided. The possibility of combining simulation software ("theory") with years of experience ("practice") of our technicians offers many advantages and reduces your costs.
* ESI ("Early Supplier Involvement"): Suppliers should participate in the design process as early as possible in order to provide supplier knowledge in a timely manner: Potential results include significant cost reduction, simplified design and/or product improvement.