Processing workshops and foundries try to produce metal castings that strictly abide by design specifications and have as little deviation as possible. However, avoiding defects in product operation can be a daunting task, as most metals shrink to a certain extent when they cool. When the component shrinks, it will severely damage the integrity of the entire device and may eventually rupture under pressure. To help reduce or eliminate the opportunity for faulty parts to enter the market, many factories use inspection equipment to detect surface and internal defects. Despite these efforts, the shrinkage of metal castings is still an important issue for many manufacturers.
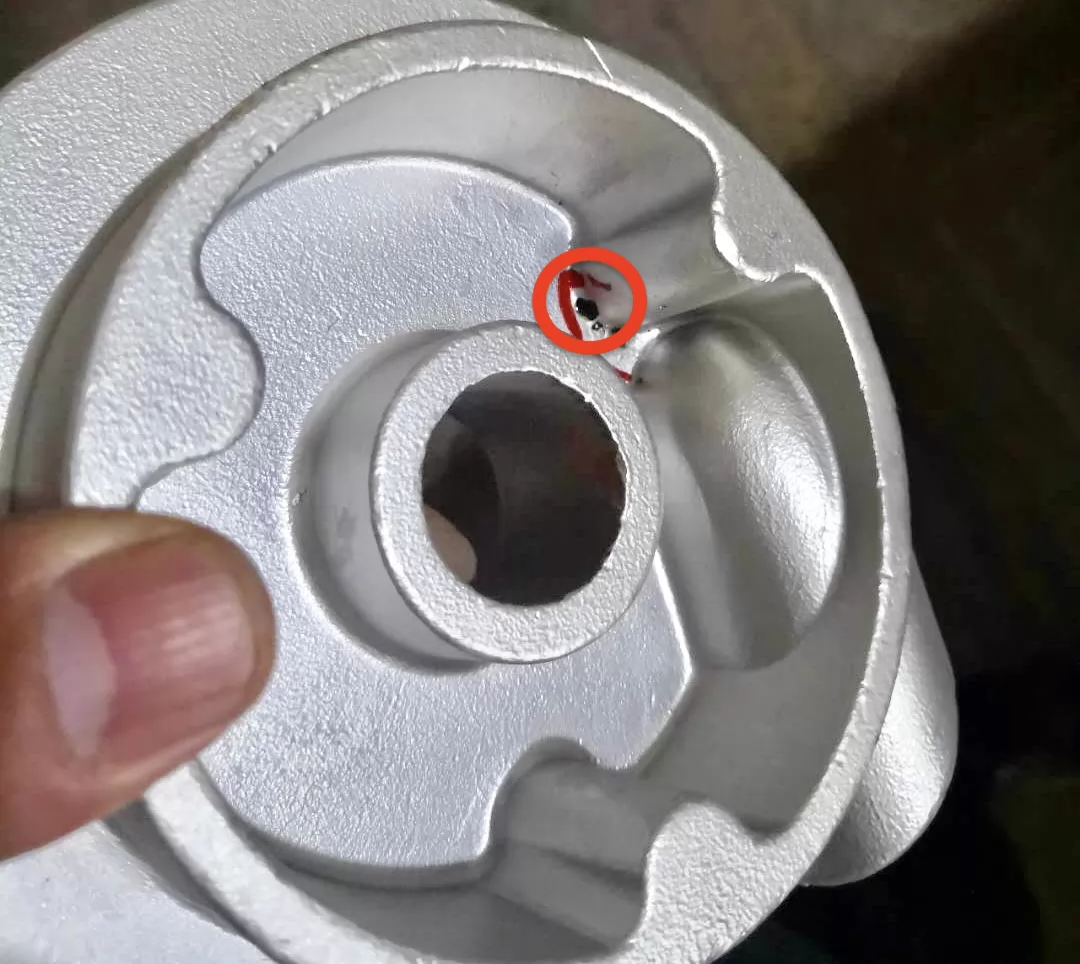
There are two main porosity problems in the foundry industry: shrinkage porosity and gas porosity. Shrinkage porosity defects refer to the cavities inside the component, they can cause the material to weaken, and if placed on the surface, they may deteriorate the appearance quality and corrosion resistance. Shrinkage is by far the most common type, and shrinkage can usually be detected on the surface of the casting through seemingly small holes or cracks. These holes may look round, but they are actually angled and tend to form branched internal cracks. Thick, multi-angle parts are most susceptible to this shrinkage, which occurs when the metal cools and solidifies in an uneven pattern. Determining the size, shape and surface of the cavity is essential for pointing out the defects that are occurring and determining their causes. However, it is important to distinguish shrinkage porosity from entrained air: pores caused by air entrainment have a circular shape, while materials lacking shrinkage porosity have inclined surfaces.
Four types of shrinkage may occur in metal castings: cavity shrinkage, sponge shrinkage, filament shrinkage and dendritic shrinkage.
l Cavity shrinkage: This defect occurs when two different sources of molten material are connected to form a common front when solidification has occurred. The lack of additional feed to fill the accumulated gaps will further exacerbate the cavity shrinkage problem.
l Sponge shrinkage: This usually occurs in the thicker middle part of the casting product and results in the formation of a thin lattice structure similar to filaments or dendrites.
l Filament shrinkage: usually a continuous crack network of various sizes and densities is formed under the thicker part of the material. It can be difficult to detect, and broken lines tend to connect to each other.
l Dendritic shrinkage: Dendritic fractures are narrow, randomly distributed lines or holes, usually not connected. They are generally thinner and less dense than filiform cracks.
1. Casting structure
Due to the thick section of the casting, the shrinkage cavity is formed due to poor feeding. The wall thickness of the casting is not uniform, and shrinkage holes or shrinkage porosity are generated at the hot joints of the wall thickness part.
Because the diameter of the casting hole is too small, the sand core forming the casting hole is heated by the high temperature molten metal for a long time, which reduces the solidification rate of the metal on the surface of the casting hole. At the same time, the sand core provides a channel for gas or atmospheric pressure, resulting in the hole wall Produce shrinkage and embroider loose.
The rounded radius of the concave corner of the casting is too small, which reduces the heat transfer capacity of the sand at the sharp corner and the solidification speed of the concave corner. At the same time, because the sand at the sharp corner has strong heating effect and high gas pressure, the gas released can be transferred to the unsolidified molten metal. Infiltration, causing shrinkage holes in the casting.
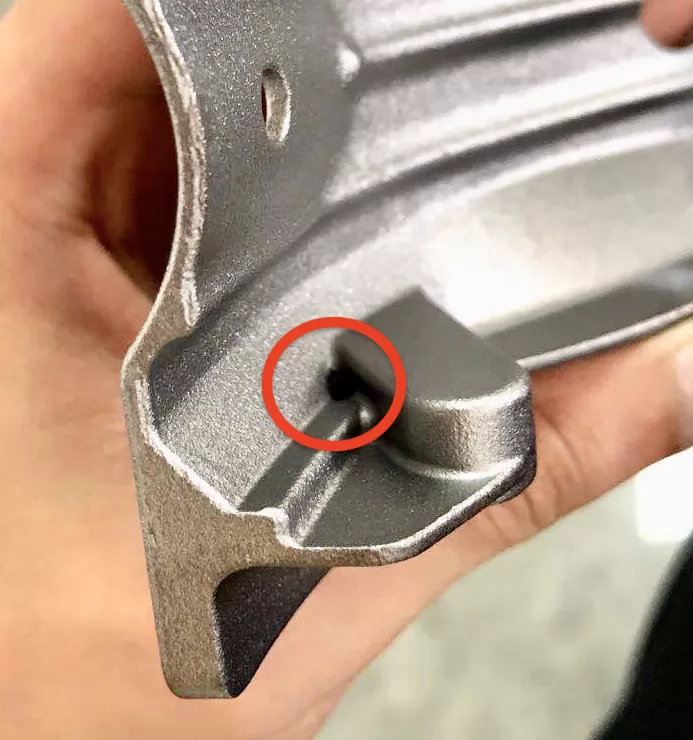
2. Smelting
The gas content of the liquid metal is too high, which leads to precipitation in the form of bubbles during the cooling process of the casting, which prevents the adjacent liquid metal from flowing to the place for feeding and shrinkage, resulting in shrinkage or porosity.
When the carbon equivalent of gray cast iron is too low, the precipitation of eutectic graphite during the solidification of molten iron will decrease, reducing the effect of graphitization expansion, increasing solidification shrinkage, and reducing the fluidity of molten iron. It is recognized that the self-feeding capacity of molten iron is reduced, so that the casting is prone to shrinkage or shrinkage.
When the phosphorus or sulfur content of the molten iron is high, phosphorus is an element that expands the solidification temperature range, and at the same time forms a large amount of low-melting phosphorus eutectic, which reduces the feeding capacity during solidification. Sulfur is an element that hinders graphitization, and sulfur can also reduce the fluidity of molten iron. At the same time, the oxidation of molten iron is serious, which also reduces the fluidity of the liquid metal, causing shrinkage or porosity in the casting.
When inoculating cast iron or ductile iron is inoculated with an inoculant such as ferrosilicon before pouring, if the inoculation is not good, a large amount of cementite will be precipitated when the molten iron is solidified, which will increase the solidification shrinkage and cause shrinkage or shrinkage.
3. Process design
(1) The design of the pouring system is unreasonable: When the design of the pouring system is inconsistent with the solidification principle of the casting, it may cause shrinkage or shrinkage of the casting. The main manifestations are improper pouring position, which is not conducive to sequential solidification, and the position and size of the inner gate are incorrect. For gray cast iron and ductile iron, if the inner gate is opened at the thick wall of the casting and the inner gate is thicker, the inner gate will be in a liquid state for a long time after pouring. Under the action of graphitization expansion caused by the solidification of molten iron, the molten iron will flow back to the sprue through the inner gate, thereby causing shrinkage and shrinkage of the casting.
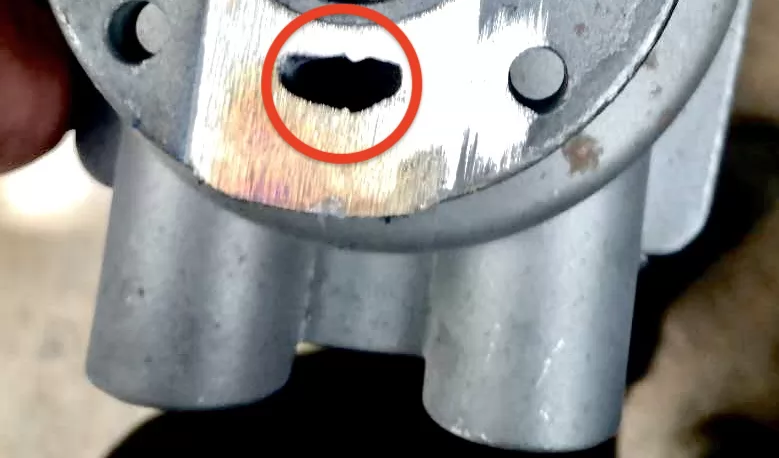
(2) The design of the riser is unreasonable: the position, quantity, size and size of the riser neck fail to promote the sequential solidification of the casting, which may cause shrinkage and shrinkage of the casting. If the air outlet riser is not placed on the top of the dark riser, or the cold iron is used improperly, it will also cause shrinkage and shrinkage of the casting.
(3) Molding sand and core sand: the refractoriness and high temperature strength of molding sand (core sand) are too low, and the thermal deformation is too large. Under the action of the static pressure of the molten metal or the graphitization expansion force, the profile wall or core wall will move. Increase the amount of feeding actually required for the casting or the appearance of new hot joints in the expansion part, resulting in shrinkage and shrinkage of the casting. This phenomenon is very sensitive to large and medium-sized castings. In addition, if the moisture content in the molding sand is too high, the thickness of the dry layer on the surface of the mold wall will be reduced and the moisture in the moisture condensation zone will increase, and the range will be expanded, thereby increasing the mobility of the molding wall, leading to shrinkage and porosity.
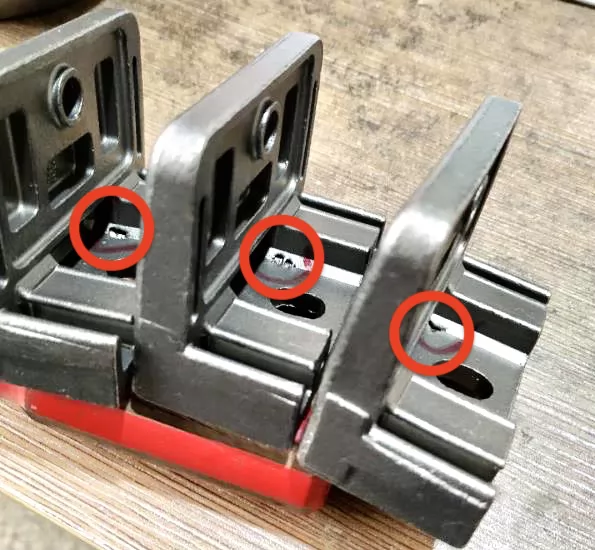
(4) Pouring: the pouring temperature is too high, which will increase the liquid shrinkage of the liquid metal; when it is too low, it will reduce the feeding capacity of the riser, especially when the bottom pouring system is used, and the castings are often Shrinkage holes and shrinkage porosity are produced in the lower part. When the riser is not filled up or the open riser is not filled with molten metal for large and medium-sized castings, this will reduce the feeding capacity of the riser and cause shrinkage or porosity in the casting.