Nickel Alloy Precision Investment Casting
At Besser Casting, we specialize in producing a wide range of nickel castings, nickel alloy castings, and nickel-based metal castings that meet the highest standards for durability and corrosion resistance. Using an advanced vacuum-assisted investment casting process, we create high-quality castings for demanding industries, including aviation, defense, and aerospace. Our nickel alloy castings are specifically engineered to withstand extreme temperatures and harsh environments, ensuring reliable performance even in the most challenging conditions. With our expertise, Besser Casting delivers precision solutions tailored to meet your unique project needs.

Besser is one of the largest nickel castings manufacturer in China. With our decades of professional nickel castings process, We provide you with customized nickel castings services to meet your precise design specifications and any required grade.
What is Nickel Alloy Casting
Nickel castings (also called Nickel Alloy castings or Nickel base alloy castings): refers to nickel-based, and other metals, such as tungsten, cobalt, titanium, iron and other metals, to make nickel-based Alloy. This nickel-iron alloy casting is the most widely used and strongest material in superalloys. It has good corrosion resistance and plasticity.
Advantages of Nickel Alloy Casting
Nickel alloy castings offer unmatched resilience, ideal for high-stress and corrosive environments across various industries. Here’s a detailed look at their advantages:
-
Superior Corrosion Resistance
Nickel alloy castings are highly resistant to oxidation and corrosion, even in chemically aggressive environments. This property makes them perfect for industries like marine, chemical processing, and oil and gas, where components regularly encounter harsh substances. -
High-Temperature Endurance
Nickel-based metal castings retain their structural integrity at elevated temperatures, making them a top choice for high-heat applications such as aerospace, automotive engines, and power generation turbines. The alloys resist thermal expansion and warping, ensuring stability and reliability in components under thermal stress. -
Exceptional Strength and Durability
Known for their robust strength and longevity, nickel alloy castings stand up to significant wear and tear, extending the service life of machinery parts even under intense operating conditions. This makes them a cost-effective option over time for industries needing long-lasting parts. -
Enhanced Mechanical Properties
Nickel alloys support complex shapes and precise detailing, enabling the production of intricate parts with high accuracy. This versatility allows manufacturers to meet strict specifications in demanding industries, producing everything from turbine blades to specialized medical implants. -
Diverse Applications
Common applications for nickel castings include turbine blades, chemical plant equipment, aerospace components, and marine hardware. Their adaptability to extreme conditions has led to broad use across sectors requiring both durability and performance under stress.
The combination of corrosion resistance, temperature stability, and high durability makes nickel alloy castings an optimal choice for sectors that rely on materials capable of withstanding demanding operational environments
Production of Nickel Castings Using the Investment Casting Process
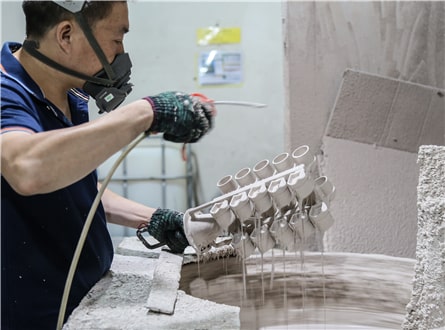
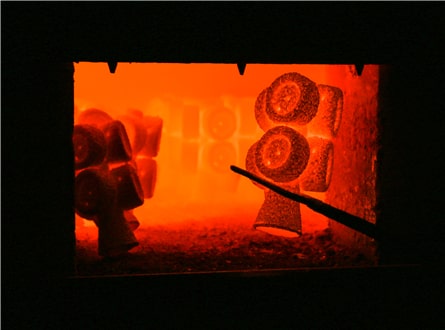
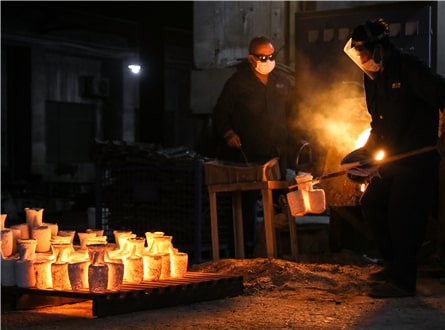
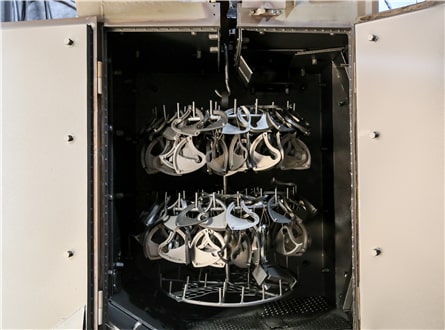
To better comprehend nickel alloy investment casting, let's outline the key steps involved in the process:
-
Step 1: Pattern Creation
The casting process begins with the fabrication of a precise wax pattern that replicates the final component's shape. Skilled artisans or advanced automated systems can create these patterns. -
Step 2: Mold Preparation
The wax patterns are then attached to a gating system, which allows the flow of molten metal into the mold. The assembly is dipped into a ceramic slurry and coated with a fine refractory material. -
Step 3: Wax Pattern Assembly
Multiple wax patterns are assembled onto a central wax sprue to create a cluster. This cluster is then invested in additional layers of ceramic slurry and refractory material, building a robust ceramic shell. -
Step 4: Shell Building
The ceramic shell is further strengthened by repeated dipping and stuccoing processes, ensuring a durable mold capable of withstanding the molten metal's temperature and pressure. -
Step 5: Dewaxing
The ceramic shell, now containing the wax patterns, is heated to melt and remove the wax, leaving behind a hollow cavity in the shape of the desired component. -
Step 6: Casting
The ceramic shell is preheated to eliminate any remaining moisture and then filled with molten nickel alloy. The alloy solidifies within the cavity, taking the shape of the wax pattern. -
Step 7: Finishing and Inspection
After cooling, the ceramic shell is broken away, and the cast component is retrieved. Finishing operations, such as removal of gating systems, heat treatment, and surface treatment, are performed to achieve the desired specifications. Finally, the component undergoes rigorous inspection to ensure quality and dimensional accuracy.
Common High Nickel Alloys
Nickel alloys are popular for their strength, corrosion resistance, and high-temperature stability, making them ideal for demanding industrial applications. Here’s a detailed look at the most common types:
-
Inconel: This nickel-chromium alloy is engineered for extreme temperature stability and oxidation resistance. It’s widely used in aerospace and chemical processing industries due to its ability to withstand intense heat without losing strength.
-
Monel: Comprising nickel and copper, Monel offers excellent resistance to saltwater and acid corrosion, which is why it’s commonly used in marine applications, such as piping systems, seawater valves, and pump shafts.
-
Hastelloy: Known for superior corrosion resistance in a variety of chemical environments, Hastelloy is a top choice in chemical industries. It resists the effects of oxidizing and reducing agents, which makes it essential for chemical reactors and pressure vessels.
-
Nickel-Copper Alloys: Blending nickel and copper, these alloys are valued for their resilience against seawater corrosion. They’re used in oil rigs and desalination plants where long-term exposure to saltwater is a factor.
-
Nickel-Iron Alloys: Nickel-iron alloys, such as Invar, are valued for their low thermal expansion rates. Their stability makes them ideal for precision instruments, optical devices, and electronic components where minimal expansion or contraction is critical.
Each nickel alloy casting offers a unique balance of durability, temperature resistance, and corrosion resistance. Selecting the right alloy can greatly enhance the lifespan and performance of components in challenging environments, from aviation to marine engineering and chemical processing.
As an excellent nickel casting service provider, we can provide a variety of commonly used nickel-based metal casting alloys. Of course, we also provide customized services to meet customers' needs for metal casting projects.
Alloy | Heat Treatment | UTS (kpsi) | YS (kpsi) | % Elongation | Hardness |
Inconel 625 | As Cast | 85-95 | 45-55 | 25-30 | Rc 25 Max |
Inconel 713 | As Cast | 110-120 | 100-110 | 3-5 | Rc 34-42 |
Inconel 718 | As Cast | 110-125 | 70-80 | 6-10 | Rc 25 Max |
Inconel 718 | Hardened | 125-135 | 110-120 | 5-7 | Rc 34-44 |
Rene 41 | Annealed | 100-110 | 90-100 | 3-5 | Rc 35 Max |
Mar-M-247 | Hardened | 135-145 | 115-125 | 4-6 | Rc 34-44 |
Haynes 230 | Annealed | 115-125 | 50-60 | 35-45 | Rc 25 Max |
Nickel X | As Cast | 55-65 | 35-45 | 6-10 | Rc 24 Max |
Application of Nickel Alloy Castings
Nickel alloy castings are used in diverse industries due to their strength, durability, and high resistance to corrosion and extreme temperatures. Here’s a look at some major applications and common products:
Applications in Various Industries
-
Aerospace and Defense: Nickel alloys are highly valued for their ability to withstand extreme heat and stress, making them ideal for jet engine components, turbine blades, and exhaust nozzles. They are commonly used in missile and rocket parts as well, where reliability in high-temperature environments is crucial.
-
Automotive and Marine: The automotive industry utilizes nickel alloy castings in turbochargers, exhaust valves, and heat exchangers. In marine applications, components such as pumps, valves, and seawater systems rely on nickel alloys to prevent corrosion and maintain structural integrity under constant exposure to saltwater.
-
Oil and Gas: The oil and gas industry often uses nickel alloy castings for pipeline valves, pumps, and drilling tools, where they face harsh chemicals, high pressures, and temperatures. Nickel alloy’s resistance to hydrogen sulfide corrosion is particularly beneficial in this sector.
-
Chemical Processing: Nickel alloy castings are used in reactors, pressure vessels, and heat exchangers to resist aggressive chemicals and oxidation. Their ability to maintain stability under both oxidizing and reducing conditions makes them essential for equipment handling corrosive chemicals.
-
Power Generation: In the power industry, nickel alloys are used in boilers, steam turbines, and heat exchangers. Nickel alloy castings withstand intense heat, making them perfect for components in nuclear power plants and other high-energy environments.
It is a key hot-end component material for modern aviation engines, spacecraft, and rocket engines, as well as ships and industrial gas turbines (such as turbine blades, director blades, turbine disks, combustion chambers, and casings, etc.). It is also a nuclear reactor, chemical equipment, coal conversion Important high-temperature structural constituent materials required by the technology and other aspects.
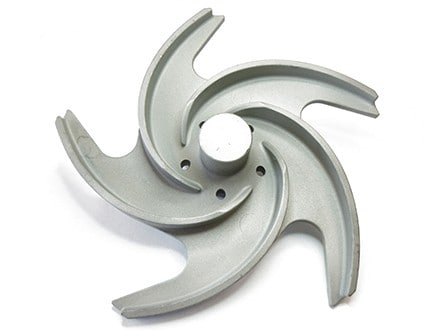
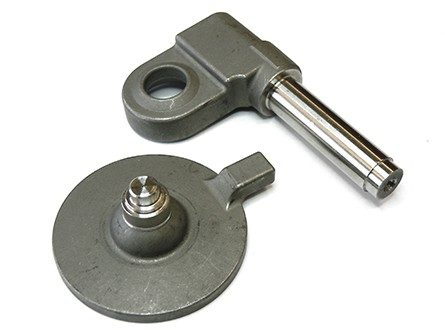
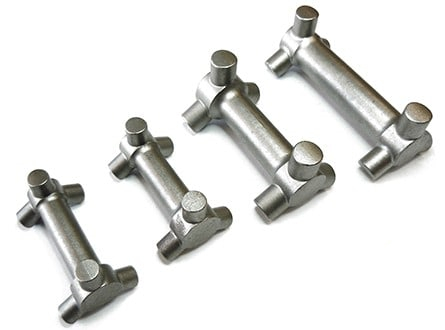
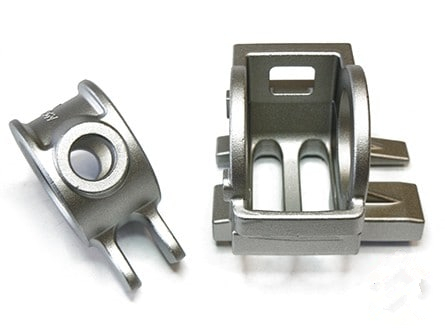
Custom Nickel Casting Services
Besser precision casting company has 18 years of casting experience. We can provide the highest quality nickel alloy castings. Our various certifications support our strict quality standards as well as testing and inspection functions. Our strong technical team can help you with any questions about nickel alloy castings.
We provide value added services to ensure your castings meet all required specifications of both the purchase order and blue prints. Services we offer include machining, heat treating, plating, assembly and hot isostatic processing.
Why choose us
- With our nickel investment casting, you can achieve intricate designs, exceptional precision and unrivaled sophistication to take your product to new heights.
- Our nickel investment casting helps you save time and money by streamlining production workflows, reducing material waste and increasing efficiency.
- With over 20 years of experience in nickel casting, embrace the future of metal fabrication with nickel investment casting, a cutting-edge technology that gives you a competitive edge and differentiates your products.
Contact us to learn more about custom nickel alloy castings.