Your Trusted Investment Casting Factory
Looking for a way to boost your project’s profits? Our precision metal casting process uses cutting-edge technology to reduce costs by 10% compared to competitors, giving you higher profit margins. If you need custom metal castings, click here to learn more and get in touch with us today!
REQUEST A QUOTE
Lost Wax Casting Process
Lost wax casting is the process of choice when producing intricate, high-precision metal parts with complex geometries. This method is favored across industries such as jewelry, aerospace, and medical devices due to its ability to achieve fine details and tight tolerances. Lost wax casting eliminates the need for most secondary operations, although post-machining may be required to meet more critical specifications. Parts produced via lost wax casting can also be finished in a wide variety of ways, just like their counterparts made through other manufacturing techniques.
Like traditional casting methods, lost wax casting requires the creation of a mold, but instead of using a rigid die, a wax pattern of the part is first made. The pattern is coated in a heat-resistant material, usually a fine ceramic shell, which hardens around the wax. The wax is then melted away, leaving behind a hollow mold that can be filled with molten metal. The metal hardens into the shape of the part, and once cooled, the shell is broken away, revealing the final metal piece.
Lost Wax Casting Services at Besser
Lost Wax Casting Services
Selecting the correct manufacturing method for your product order is critical. Lost wax Lost Wax Casting is the right choice when you need high precision, complex parts.
This method proves to be cost-effective as it requires fewer separate processes, saving both time and money during production.
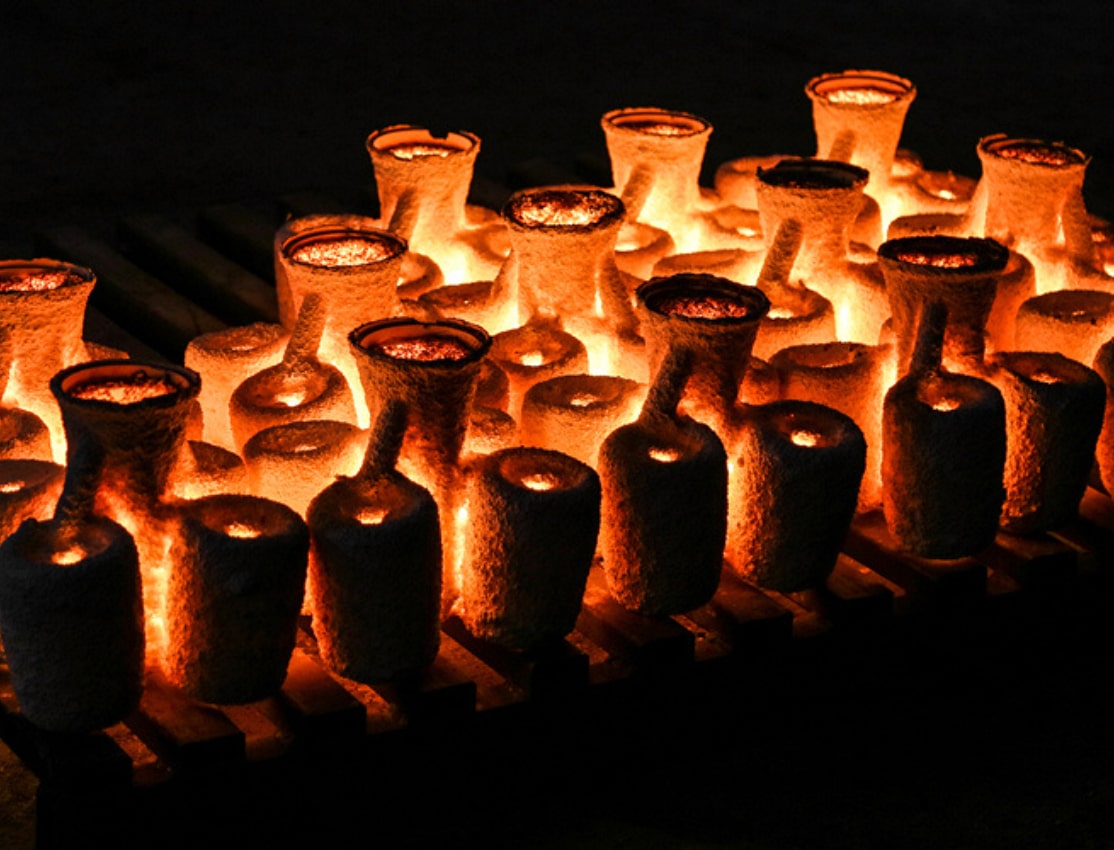
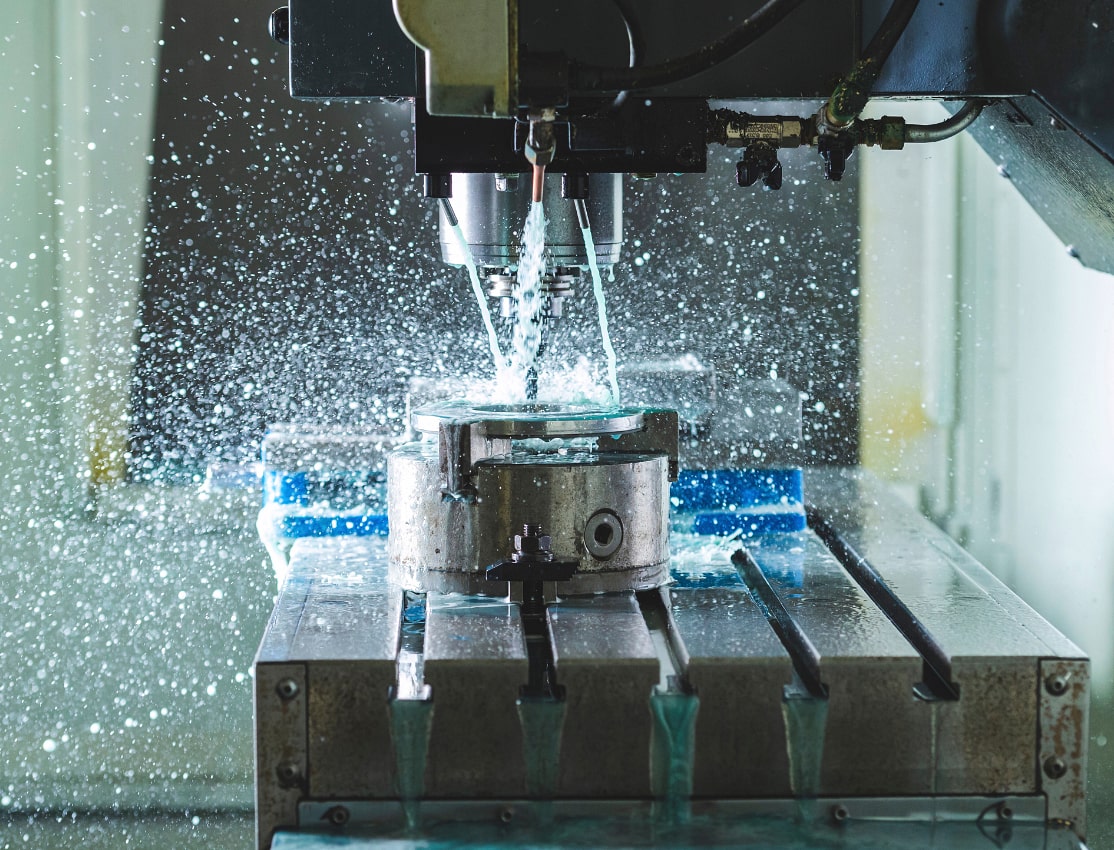
Machining Services
Our state-of-the-art facilities, equipped with the latest advanced technology and machinery, enable us to provide our clients with a full range of comprehensive machining services. These include precision milling, turning, boring, grinding, drilling, wire cutting, as well as custom solutions tailored to meet specific project requirements.
Surface Treatment Services
We offer various types of surface treatments to enhance the performance, wear resistance and service life of the metal components we produce.
● Shot blasting | ● Sand blasting |
● Vibration grinding | ● Electro-galvanizing |
● Pickling and passivation | ● Electropolishing |
● Phosphating treatment | ● Blackening treatment |
● Brush polishing | ● Mirror polishing |
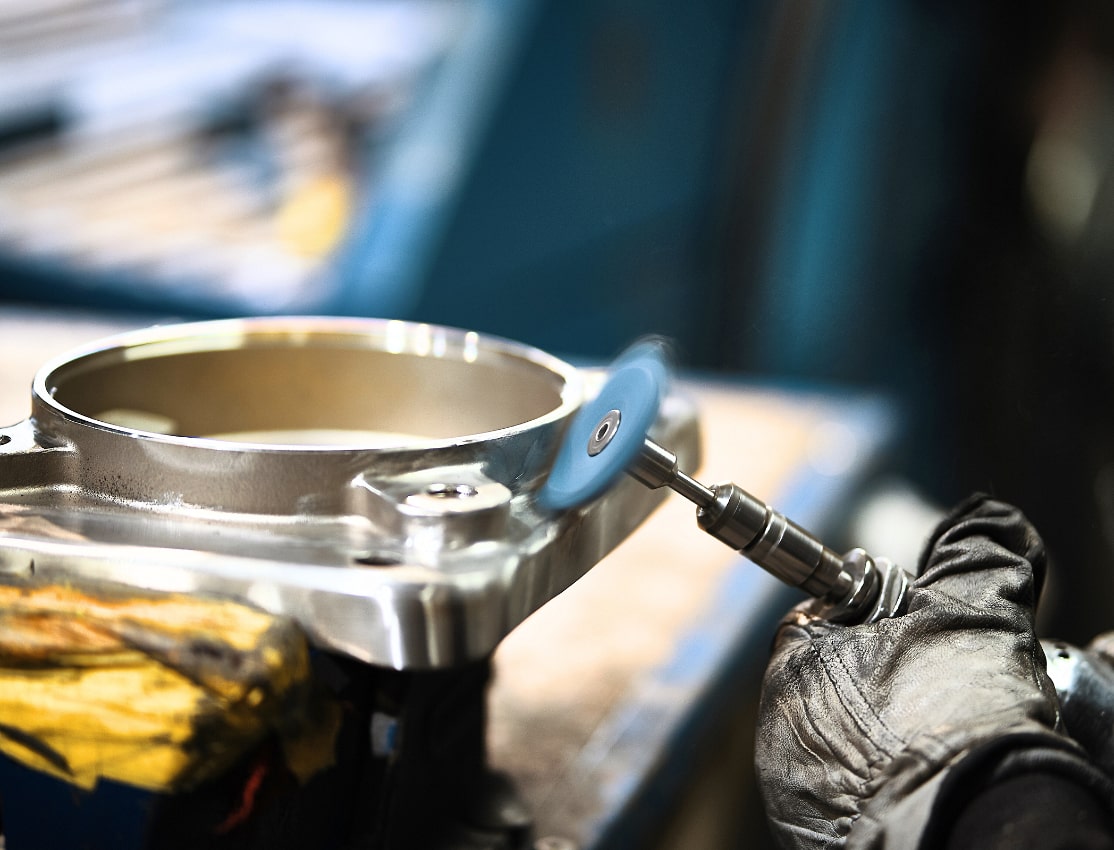
Main Applications of Lost Wax Casting Process
Lost wax casting is known for its precision and ability to produce highly intricate metal parts, making it suitable for a wide range of applications across various industries. The process excels at creating small to medium-sized components with fine details, especially when high accuracy is required. It is particularly useful for industries such as jewelry, aerospace, medical devices, and industrial machinery. Lost wax casting is ideal when complex shapes or fine features are needed, and it can handle metals that are difficult to cast using other methods.
- Aerospace & Medical Components
- Jewelry and Decorative Items
- Industrial Machinery Parts
- Turbine Blades
- Dental Implants
- Precision Tools and Components
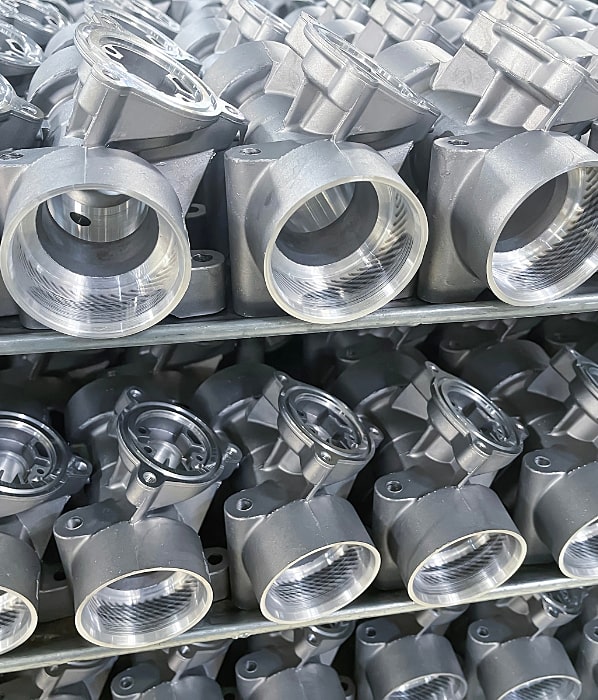
Advantages And Disadvantages of Lost Wax Casting
Lost wax casting offers several benefits, especially when precision, intricate details, and complex shapes are required. However, like any manufacturing process, it has some limitations that need to be considered. Below are the main advantages and disadvantages of lost wax casting.
Advantages of Lost Wax Casting | Disadvantages of Lost Wax Casting |
---|---|
High Precision and Detail: Lost wax casting can produce highly detailed and complex parts with tight tolerances, making it ideal for applications in industries like jewelry, aerospace, and medical devices. | High Cost for Small Production Runs: The initial setup costs, including creating wax patterns and the ceramic shell, can be high. This makes it less cost-effective for small-volume production runs compared to other methods like die casting or sand casting. |
Versatility in Materials: A wide range of metals can be used, including precious metals, stainless steel, aluminum, and high-temperature alloys, allowing for diverse applications across multiple industries. | Labor-Intensive Process: Lost wax casting involves multiple steps, including pattern creation, shell formation, and metal pouring, which can make the process time-consuming and labor-intensive. |
Ability to Create Complex Geometries: The process can create intricate shapes that would be challenging or impossible to achieve with traditional machining methods or other casting techniques. | Material Limitations: While many metals can be cast using lost wax casting, some materials with extremely high melting points or special requirements may not be suitable for the process. |
Minimal Waste: The process produces very little waste material, making it an efficient method for high-quality parts. The excess wax can be reused in subsequent casting cycles. | Size Limitations: While lost wax casting is excellent for small to medium-sized parts, it may not be the best choice for large-scale castings due to the challenges in creating larger molds and the difficulty in handling molten metal for big parts. |
Smooth Surface Finish: Lost wax casting typically results in parts with a smooth surface finish, reducing the need for additional post-casting machining and finishing. | Complexity of Mold Creation: The creation of the ceramic shell around the wax model requires skill and precision, and any defects in the shell can lead to casting failures, particularly with intricate designs. |
Why Choose Besser for Online Lost Wax Casting Services?
● The geographical position is good, we are located in a coastal city, and can deliver products quickly.
● The production cost is low. We have decades of production experience, which can reasonably reduce your unnecessary losses. Make your products more competitive
● Professional technical team, we have a technical team and hundreds of skilled workers can help you solve various problems very well.
● To support various processing services, we have two factories, one for production and one for processing.
● After-sales service, we have online customer service to ensure that you can answer you in time when you need help.
Lost Wax Casting Process
Lost wax casting enables a manufacturer to reproduce models in exact detail. Essentially, it involves duplicating an item in wax, then “losing” the wax to create a space for molten metal.
“Lost wax” casting occurs in two basic forms: solid core or hollow-core reproduction. The manufacturer creates either a solid wax model (for solid core patterns) or a wax copy of a clay model (for hollow core patterns).
Operation Process of Lost Wax Casting
Lost wax casting requires multiple steps to be completed.
1. Model making.
The manufacturer creates the original model with wax, clay, or other materials. Waxes and oil-based clays are more commonly used because these materials are relatively soft.
2. Reverse mold.
Use the original model to mold. Generally, there is a rigid outer mold plus a softer inner mold, and the inner mold is the exact negative shape of the original model. The inner mold is usually made of latex, urethane rubber, or silicone and supported by the outer mold. The outer mold can be made of plaster, but it can also be made of fiberglass or other materials. Most molds are made of at least two pieces, and during construction, some spacers are placed between the parts so that the mold can be accurately put back together. If there are long and thin parts that extend out, they are often cut from the original model and molded separately. Sometimes many molds are needed to reconstruct the original model, especially for large models.
3. Cast wax.
Once the mold is complete, pour the molten wax into it and shake it to form a uniform coating on the inner surface, usually about 1/8 inch (3 mm) thick. Another method is to fill the entire mold with molten wax and let it cool until the desired thickness is set on the surface of the mold. Then pour out the rest of the wax again, invert the mold to cool and harden the wax layer. Using this method is more difficult to control the overall thickness of the wax layer.
4. Remove wax.
Remove the hollow wax version of the original model from the mold. The mold can be reused to make multiple copies, which is only limited by the durability of the mold.
5. Polishing.
Polish each hollow wax replica and wipe the parting line with a heated metal tool. The surface of the wax model should not have any defects, it looks like a finished product. The individually molded wax molds can now be heated and combined together.
6. Open the sprue.
The wax replica is made into a wax tree with a tree-like structure, which will eventually provide a path for the molten casting material to flow and allow air to escape. There is usually a wax "cup" from the top, and the wax mold is connected to various points by wax pillars.
7. Sizing.
The wax tree is immersed in silica slurry and then immersed in sandy plaster or crystalline silica with a certain grain size. The combination of slurry and gravel is called a ceramic mold. Dry and repeat the process until at least half an inch of coating covers the entire part. The larger the object, the thicker the shell needs to be.
8. Burn out.
The ceramic shell coating is placed in the kiln, and the heat hardens the silica coating into a shell, melting the wax and expelling it. The melted wax can be recycled and reused, but it is generally simply burned. Now, the shape of the original object is the inside of the hardened ceramic shell, which is the negative shape previously occupied by wax. The feed tube is now also hollow.
9. Test.
Let the ceramic shell cool down and then test to see if water will flow freely through the feeder and exhaust pipe. Cracks or leaks can be repaired with thick refractory paste. To test the thickness, holes can be punched in the shell and then patched.
10. Pouring.
Reheat the shell in the kiln to reinforce the patch and remove all moisture, and then put the mouth up into a bucket full of sand. The metal is melted in a crucible in the furnace and then carefully poured into the shell. The enclosure must be very hot, otherwise, the temperature difference will destroy it. The filled shell is then cooled.
11. Demoulding.
The shell is knocked off, removing rough castings. The metal gate is also cut off and recycled for the next pouring.
12. Metal polishing.
Finally, metal casting is polished.
Lost Wax Casting Manufacturer
If you are looking for a lost wax casting manufacturer to help you produce various metal products. Then you may need our besser casting to serve you.
We are a precision casting company from China, and our best casting process is lost wax casting. Our current casting products are mainly exported to more than ten countries, including the United States, Germany, Japan, Spain, the Netherlands, Italy, South Korea and Brazil. So far, we have become an important Chinese supplier to two of the world's top 500 companies, and a designated supplier of many industrial giants.
Contact Besser Lost Wax Casting Manufacturer
Contact us today to learn more about this industry-leading industrial manufacturing process. Learn how we can work with you to increase the efficiency of mass order production without losing the precision performance that makes your company stand out.