With the continuous development economics and industry, people's demand and requirements for products have gradually become larger and higher. In the meantime, the ability of precision dewaxing casting technology to solve complex structures of products has been recognized by the industry. Common precision dewaxing casting processes include water glass process, silica sol process, composite type process, etc. Among them, the silica sol process has achieved the highest casting quality and the lowest processing rate among many processes. It is also due to its high density that it is widely used in casting products such as small and medium-sized parts and extra-small parts.
As introduced in the previous article in our blog, the process steps of silica sol dewaxing casting are divided into:
Pressing wax (wax injection molding)—wax repair—wax mold inspection—group tree (wax module tree)—shell making (first dipping, sanding, then second dipping, and finally air-drying mold shell)—dewaxing (steam dewaxing)—mold shell roasting—chemical analysis—casting (pouring molten steel in the mold shell)—vibrating shelling—casting and pouring rod cutting separation—grinding gate—shot blasting
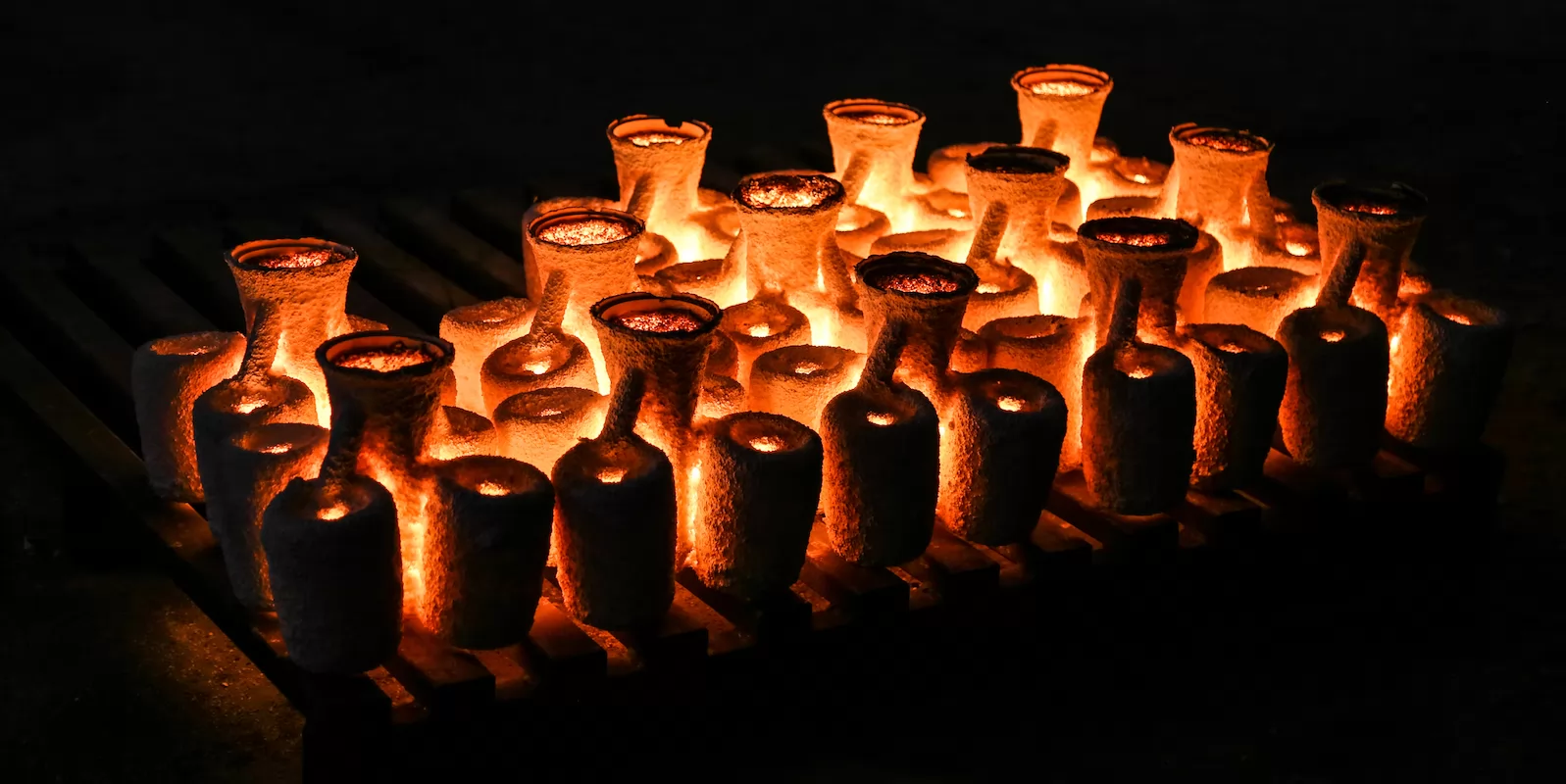
It can be seen that half of the processes are related to wax molds. Since the accuracy tolerance of silica sol dewaxing casting can be guaranteed to CT6, which means the smallest tolerance accuracy is only plus or minus 20 filaments. Therefore, the requirement for the shrinkage rate of the wax mold used in the process is very high. In all steps, the shrinkage rate of the wax mold is closely linked to the size of the later product. As a result, the quality of the wax mold is one of the important factors that directly affect the quality of the casting product. The size of the wax mold directly determines the size of the finished product after casting the mold shell in the later stage. Therefore, in the silica sol dewaxing casting process, green medium temperature wax with higher stability is usually used. Whereas water glass and composite dewaxing casting process generally use white low temperature wax which is more advantaged in terms of cost.
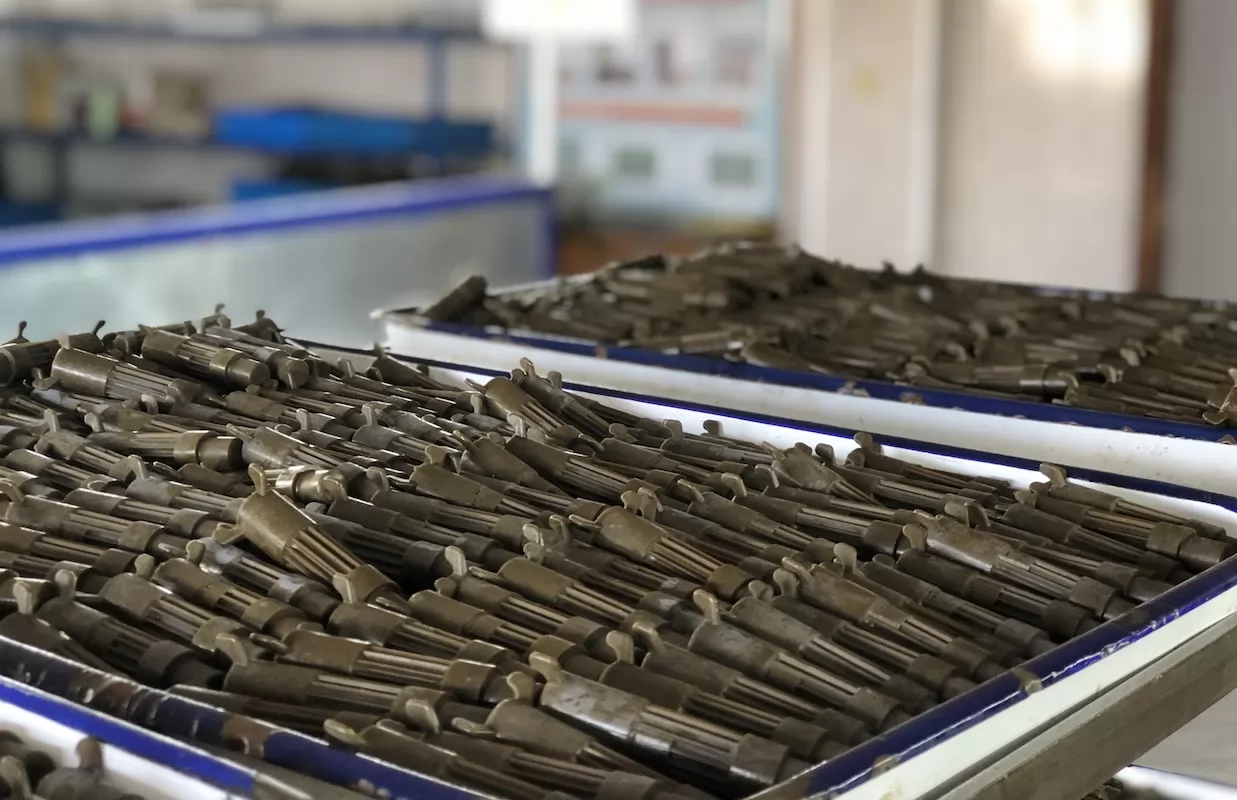
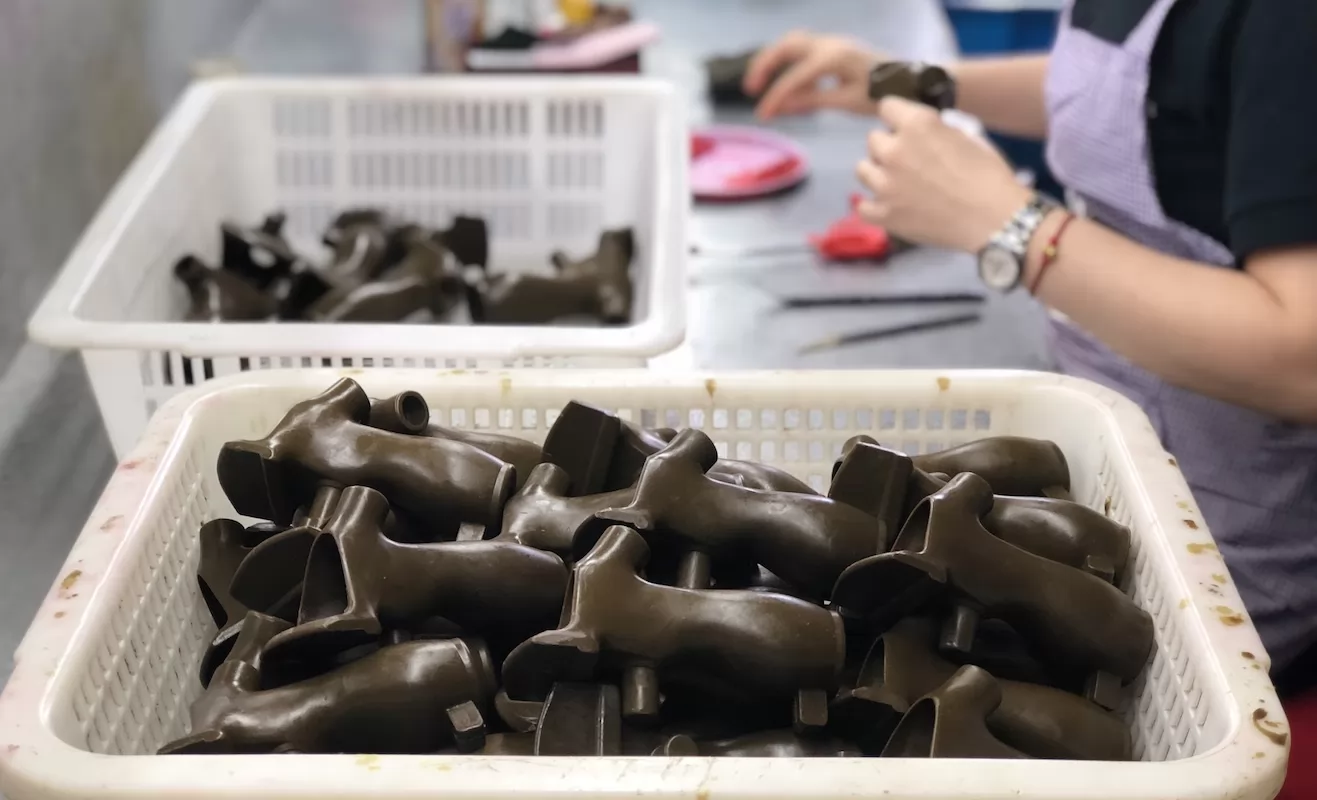
In this article, we will elaborate on the stability control method using medium temperature wax which is adapted by Besser Casting.
After a long time of use in high temperature, some components of the material of medium temperature wax will be oxidized and deteriorated. In addition, metal ions will also enter the wax material to make the wax worse and contain more impurities. What’s worse, the shrinkage rate of the wax is very different from that of the new wax. Since shrinkage rate is different from solid impurities, it is difficult to completely solve it by precipitation dehydration or filtration alone. The factory must regularly remove part of the old wax and supplement the new material to ensure the overall stability of the wax performance. When the shrinkage rate fluctuates greatly, it is necessary to isolate a part of the wax, and increase the input ratio of new wax to neutralize the wax shrinkage rate. At present, there are professional medium temperature wax manufacturing plants that can regenerate waste wax. Because of the special impurity removal process, the ash content in the regenerated wax can be lower than that of the original new wax, and other properties can be adjusted at will. Generally capable companies will also equip their own factories with a set of systemic medium temperature wax degrading and dewatering device, which greatly stabilizes the shrinkage rate of medium temperature wax. It can be seen that different factories have different treatment methods and different wax shrinkage rates. Therefore, sometimes in order to save costs, when customers change suppliers, they directly send the molds of the original suppliers for us to use. The samples must be tested to make sure that the size of the final product meets the requirements of the drawing. In a few cases, it will be necessary to modify the size of some molds due to the difference in wax shrinkage rate.
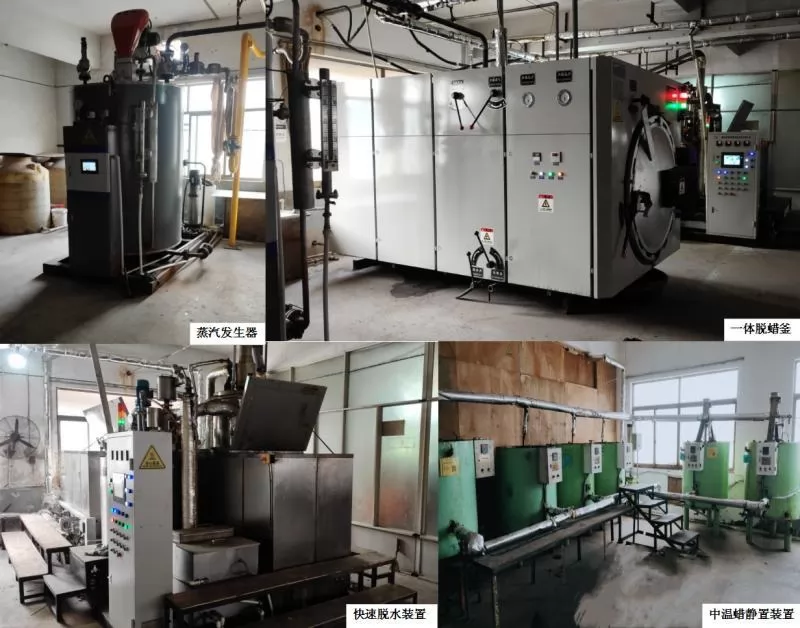
In order to strictly and stably control the shrinkage rate of the medium temperature wax, the quality of the medium temperature wax is very important. We need to control the wax material from the source, reduce the impurity content, pay attention to the process of treatment and use of wax, and do not allow high temperature treatment to extend the use life of wax material. In order to achieve real-time control of the shrinkage rate of medium temperature wax, the factory will customize a mold dedicated to the size measurement of wax parts, and set a designated wax injection machine. What’s more, professional staff are assigned to operate the machines in strict accordance with the specified parameter settings. Meanwhile, the commissioners will measure the wax mold and record the data every day, and compare the recent data to confirm whether it is necessary to make adjustments to the current operation.
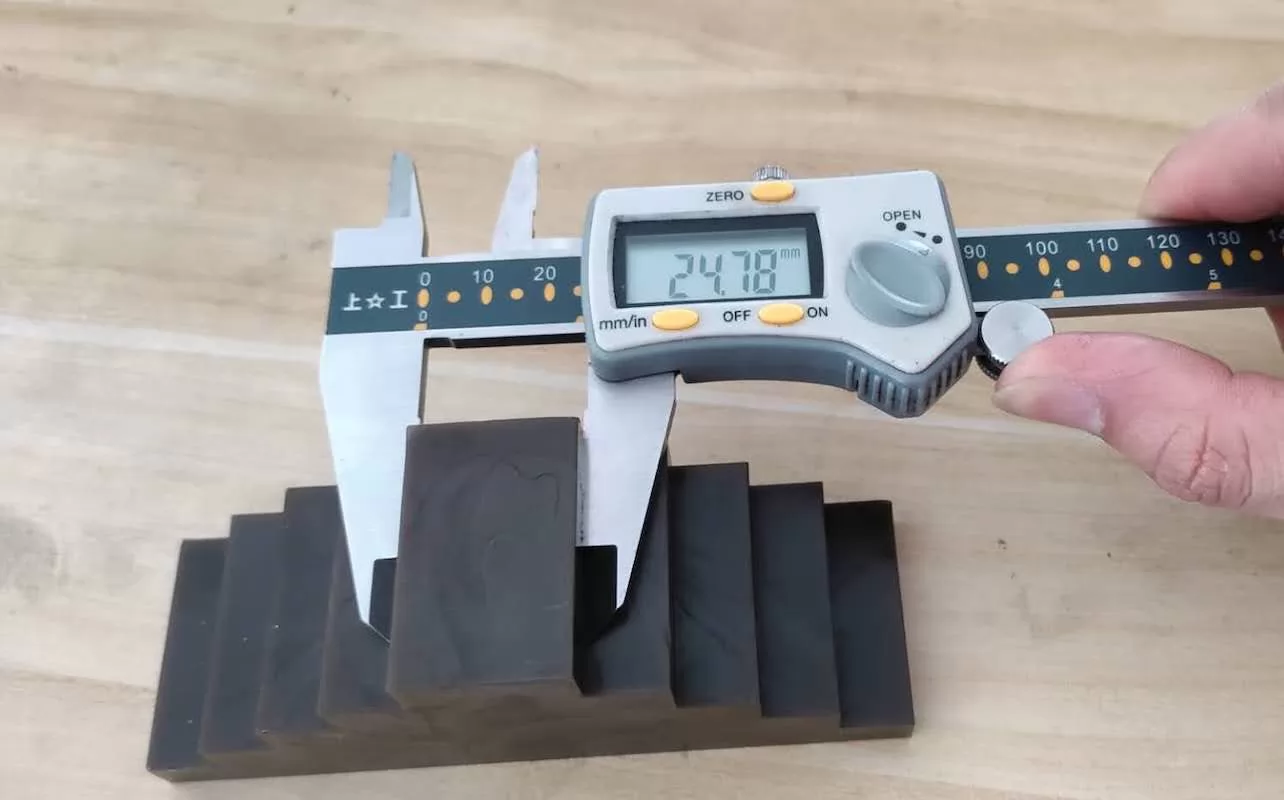
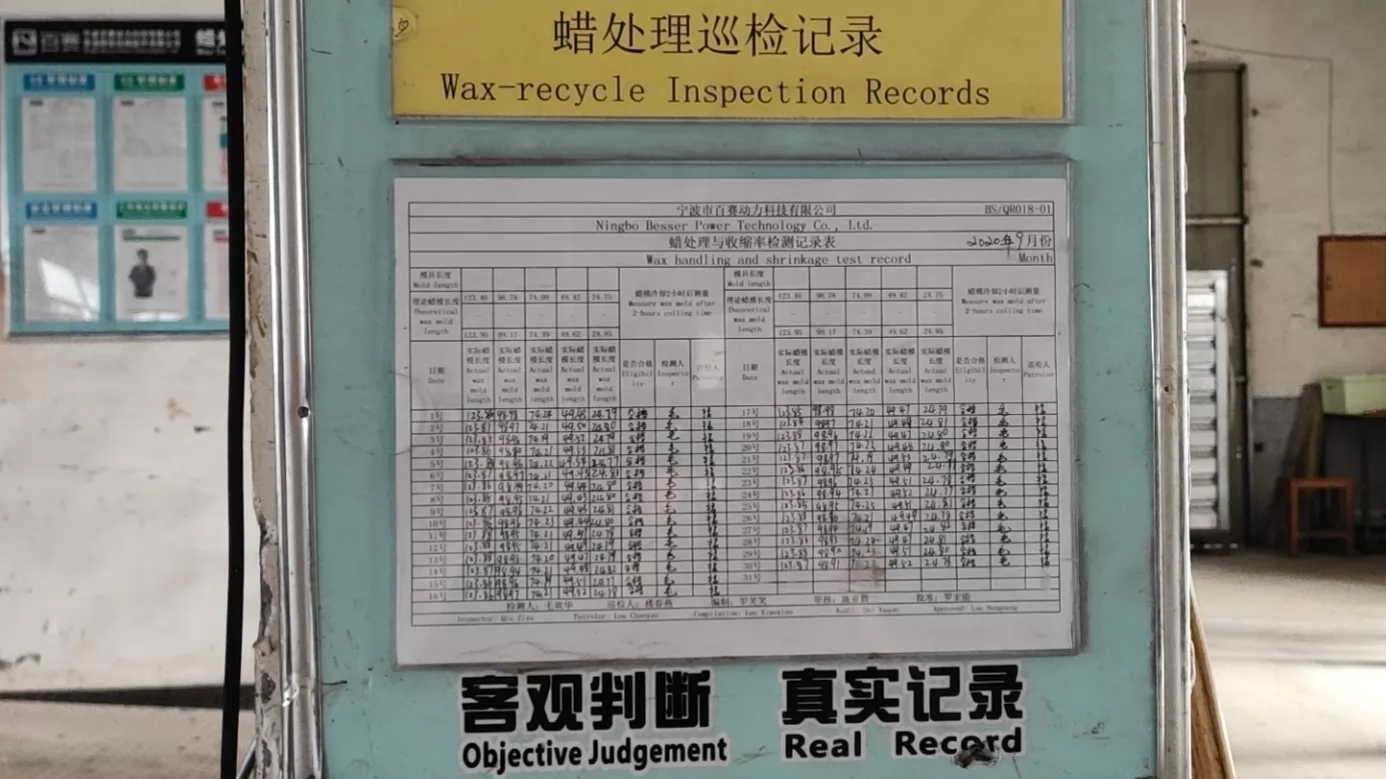
In addition to the above control and supervision, in daily production, in order to achieve the control of the finished wax film size, the setting parameters of the wax injection machine need to be set in strict accordance with the values given by the technical department. Since the medium temperature wax has a higher temperature during injection, it will shrink slightly after cooling and molding, which means its size will also vary slightly. If the values of temperature, pressure, and time during wax injection do not match, it will directly lead to the loss of wax size control.
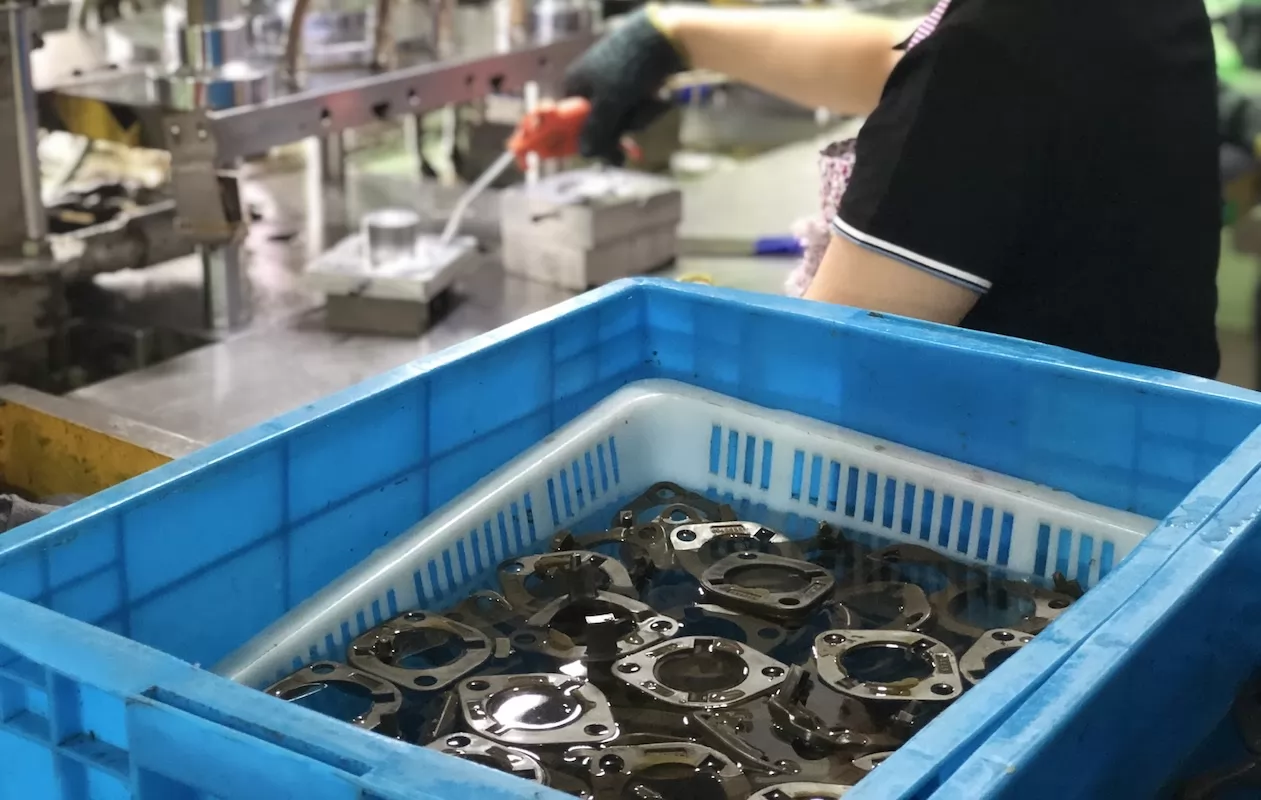
Besser Casting is not only committed to providing customers with provocative casting solutions, but also committed to providing customers with stable mass product quality. The latter one is our purpose of strict process control, which includes the wax shrinkage rate discussed in this article.