As we have introduced in the previous articles, the silica sol casting process mainly has four major processes: wax making, shell making, pouring, and post-processing (specifically, it can be subdivided into more than 20 processes). The responsibilities of technicians are not only to fully control the process standards of each process of the product, but also to understand the customization needs of customers. At the same time, we need to lead the development of new products and solve technical problems in the casting process. The most critical daily work is to carry out new processes and new technology trials to continuously improve the quality of castings, reduce waste losses and reduce manufacturing costs.
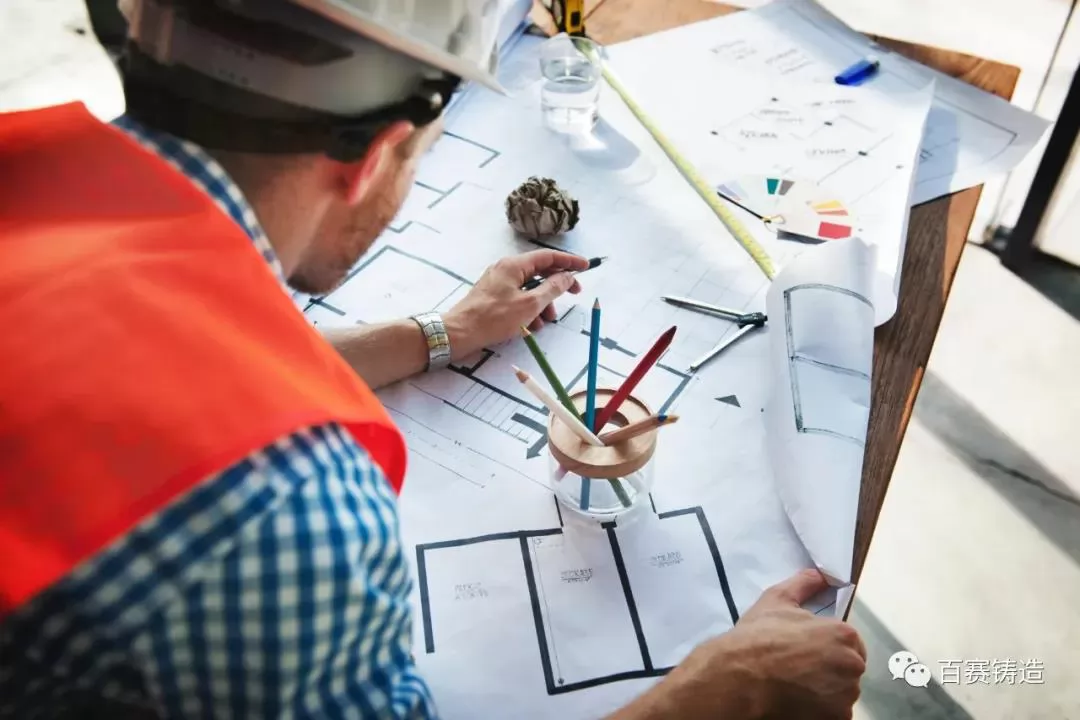
Once a technician with such an important responsibility makes a mistake in the work, the consequences will be very serious. Below I will introduce the mistakes made by our company's technicians as examples:
Mr. H, a technician of a company, docked the product A of company S from the very beginning (from sample to small batch trial order). After the sample was delivered to the customer, the mold size was not changed according to the customer’s feedback requirements for the sample. What’s worse, Mr. H did not submit the modified samples to the customer for confirmation again, which caused assembly problems in the customer for subsequent small batch products. It was lucky that we were forgiven by the customer after communication. As a result, we only compensated the replacement price of matching assembly parts, totaling more than 4000 dollar. However, this accident still had a very serious impact on the customer's delivery time.
Mr. H, a technician of a company, failed to comply with the packaging requirements, causing the surface of customer K’s sample C to be severely bumped during transportation and unable to deliver the sample to the customer in time. Although customer K agreed to let us sample again after communication, it disrupted the customer’s original plan, which seriously affected the delivery time and also affected the customer K's reputation with the final customer.
Mr. Z, a technician of a company, did not clearly specify the machining surface requirements when tracking the products D of company M, which caused the quality department to approve the shipment of unqualified products. As consequence, the customer did not accept the unqualified products and needed to return them to the factory for reprocessing. The company not only lost the extra round-trip freight, but also affected its reputation and customer delivery.
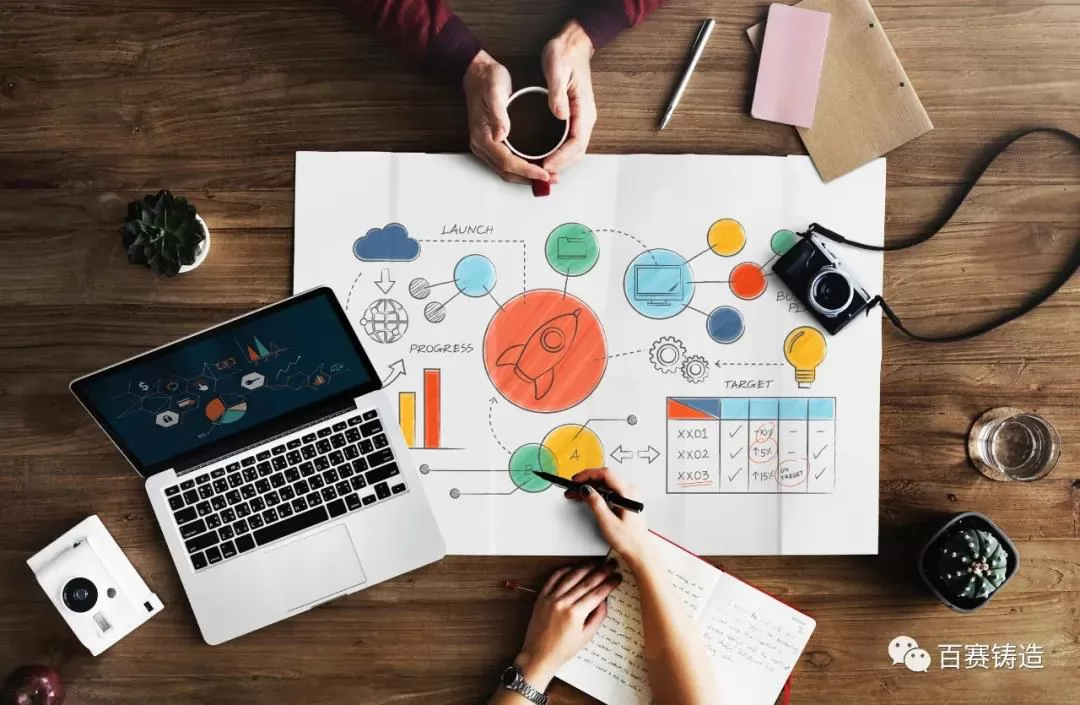
The negligence of technicians will generally cause the following losses to the company:
1. Economic loss: The unqualified products produced by the company will lead to returns and even claims from customers, consequently causing very large economic losses to the company.
2. Reputational loss: Unqualified products not only cause economic losses to the company, but also damage the company’s reputation, which is a more serious problem than the former one. A company without reputation is like a person without honesty, which will cause a large number of loss of customers and affect the survival of the company.
3. Legal Liability: Once the unqualified products enter the market and cause casualties, the company will face a more serious problem.
How to avoid the occurrence of the negligence of technical staff is also a problem that every enterprise needs to solve.
1. Strictly implement the company's IATF16949:2016 and ISO9001:2015 quality management standard documents, and use process management to avoid human errors. Mistakes are not terrible. What is really terrible is making mistakes repeatedly. All we need to do is analyze the process and results of each problem, find details and rules from it, and fill the loopholes.
2. Horizontal control and establishment of a reporting mechanism. Each employee should record the main content of the day's work, upload it to the work group as a work log, and then uniformly reviewed by department leaders to check for deficiencies. Let every team member develop good working habits, execute efficiently, be cautious, and not procrastinate or delay.
3. Cultivate team culture. For example, if Mr. H fails to complete the formulation of standard documents in time, team members will urge him to complete it efficiently, because everyone knows that if any tiny error occurs, there may be huge problems after. It is better to complete every work meticulously in the early stage and establish a rigorous work attitude, so that the team can smoothly deliver orders to customers.
4. Strengthen the sense of service, do our utmost to solve the requirements of customers, and always keep in mind the belief that customer comes first in the work.
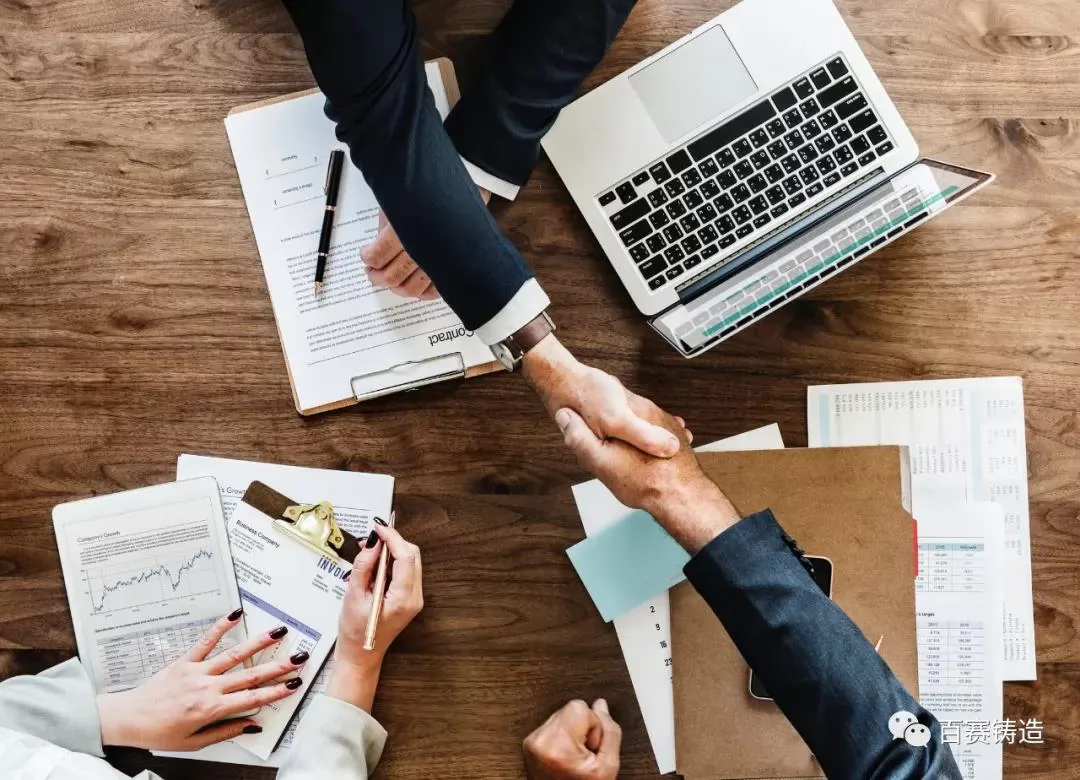
Facts have proved that those successful companies decide their success or failure in accordance with the details, and strictly discipline themselves by the spirit of craftsmanship. We should establish a strong sense of prevention, strive for excellence in product process optimization, persevere in pursuit, and strive to do so in product services. Only by taking customer needs as the guide can we run the company well, stay ahead courageously, and go higher and farther.
It is impossible to run a successful company without good staff. We hope that we can all be reliable and trustworthy in our work, avoiding causing problems to the company, and even providing predictive solutions to the possible problems.