With the introduction of silica sol shell production technology in China, China's investment casting production has achieved rapid development and great progress. In response to the development of the casting industry in recent years, the competition within the industry has become more and more fierce. Comparisons are being made in terms of raw materials, equipment, craftsmanship, etc., and customers have higher and higher requirements for the quality of castings. Therefore, our company, Besser Casting also switched from water glass process to the silica sol process in 2008, and has made breakthroughs and innovations in some technologies.
Due to limited space and experience, only the bits and pieces of experience that came from the practice in production and achieved practical results are summarized. If you have other opinions, you are welcome to write them down in the comment area.
There are many reasons for iron clamping in castings, which can be analyzed from the three aspects: welding, shell making and casting. Among the three, shell making is the most critical. Therefore, first we analyze the causes of iron clamping from the aspect of shell making:
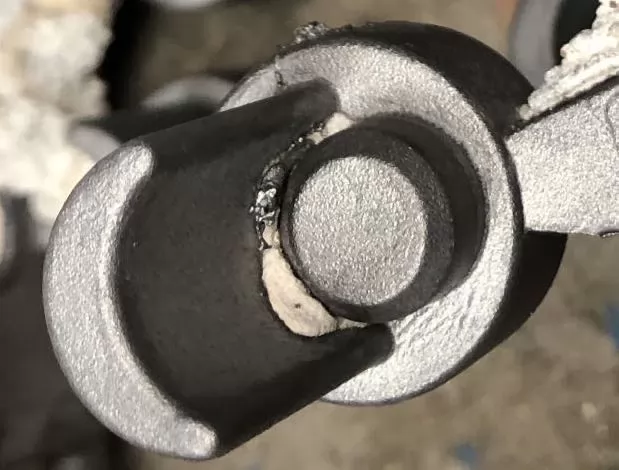
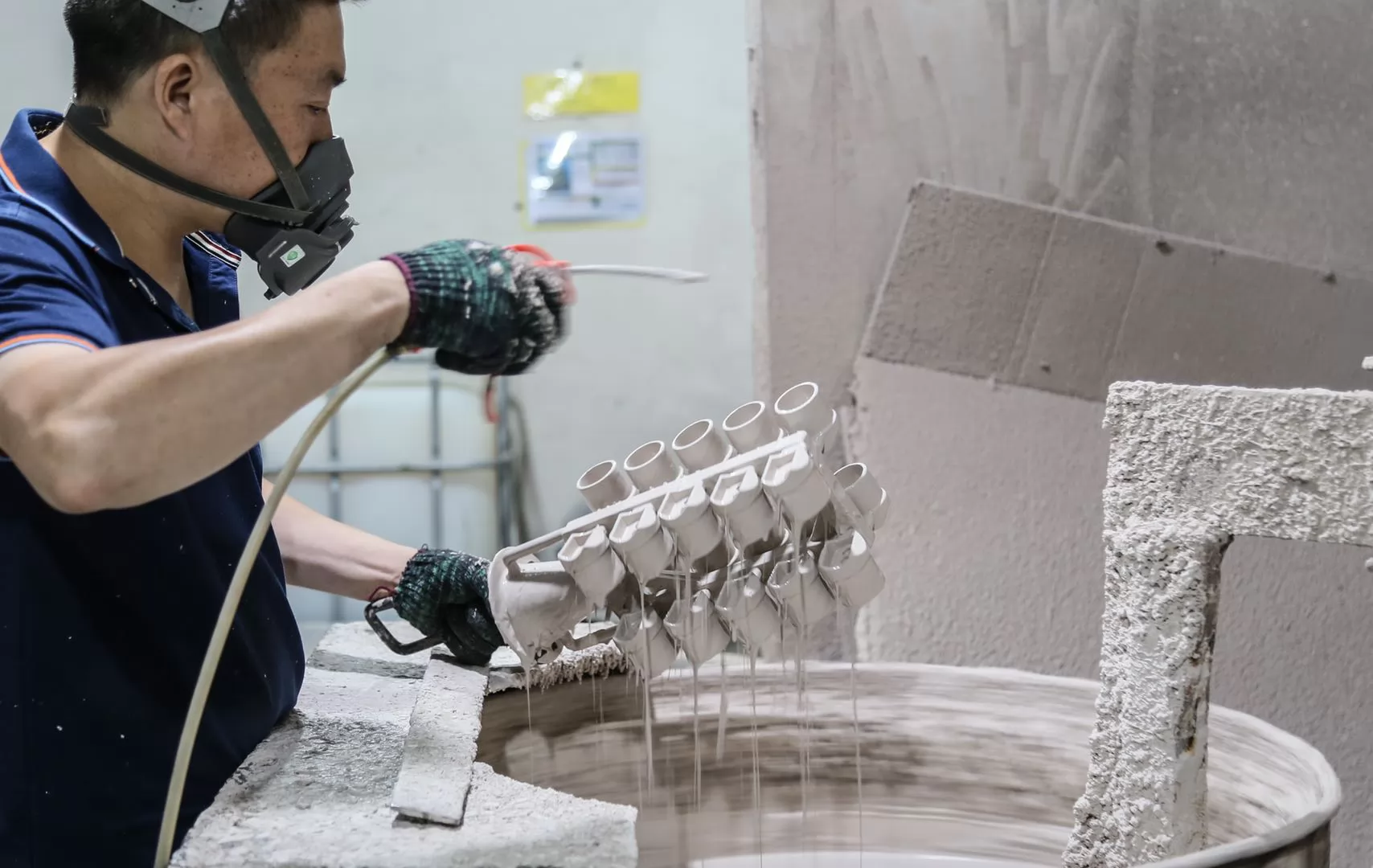
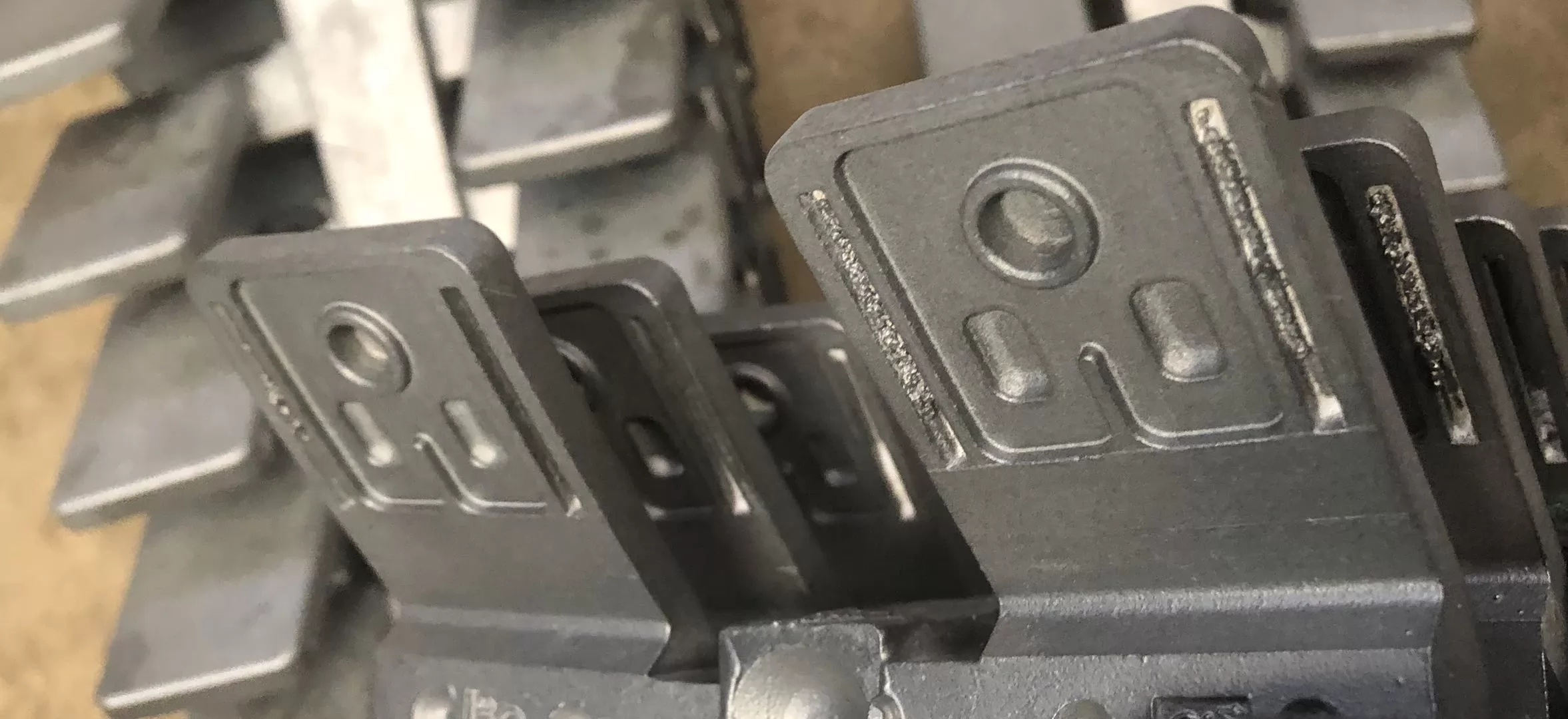
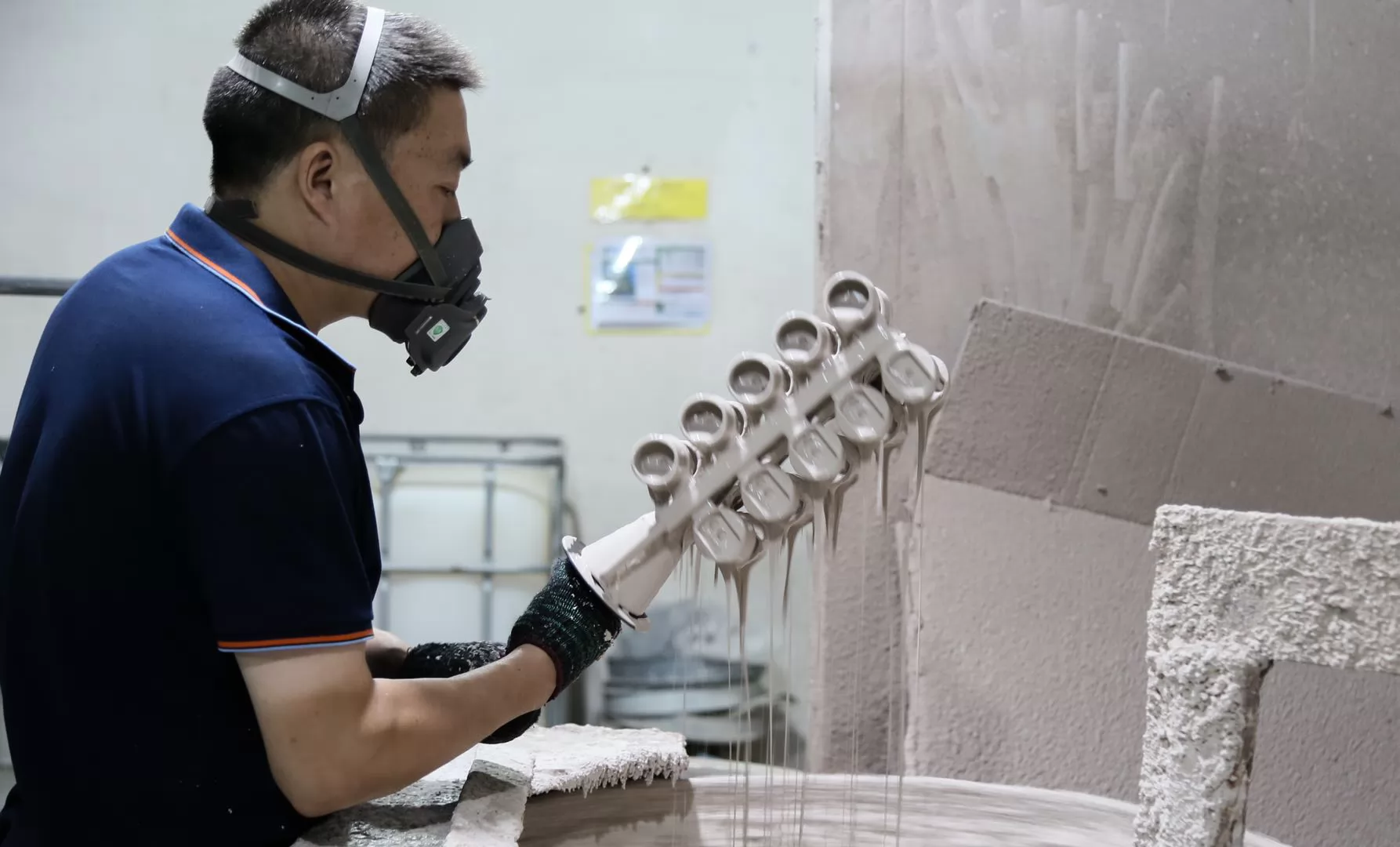
Note that the surface layer should not be too dry, otherwise it will cause the casting to bulge. A humidifier can be placed between the surface layers to maintain humidity. For different product structures, the drying time is different. We need to plan the parking time in the workshop scientifically and reasonably. For this reason, Besser Casting has also specially equipped with humidity detectors and anemometers to help employees judge whether the mold shell is dry.
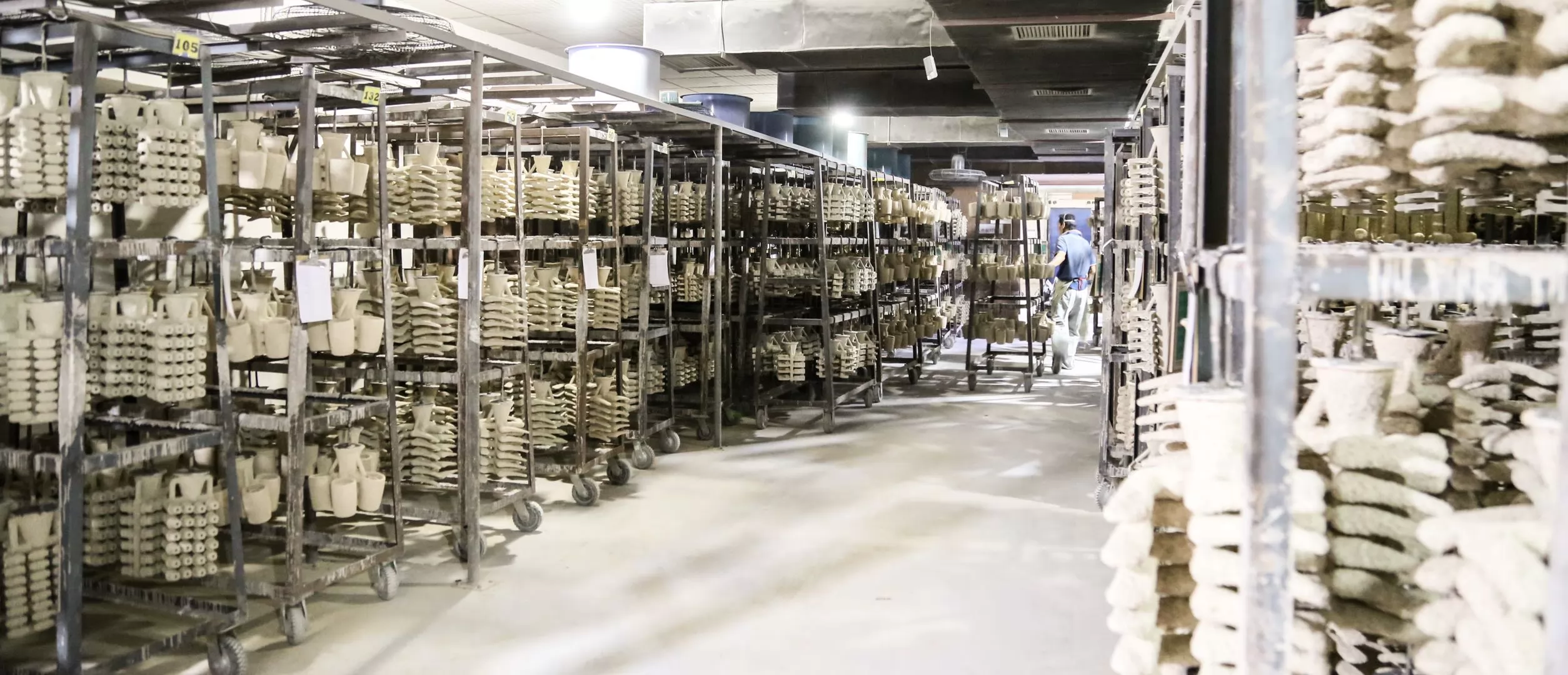
Next, let’s talk about welding. It does not directly lead to iron clamping in the product. However, due to the unreasonable welding process, it will increase the difficulty of the shell making operation. As a result, the iron clamping rate of the product will increase. In order to maximize the benefits, it’s common for factories to assemble full products on a square die. However, although the production rate is high, the product group is too dense, which will prevent the grout sand from entering. The thickness of the shell between the gate and the wax rod is not enough. Without a certain strength, the molten steel will leak when it is flushed by molten steel. Therefore, the gap between the products should be arranged reasonably. Besides, for products with deep-hole grooves, the complex side must face up or back to the wax stick, so as to facilitate leaching, blowing and drying. The salaries of shell workers are based on the number of products they make. They cannot waste too much time and energy on a series of products. For them, the more they do in the same time, the more they take. Thereby, we should also improve the welding method so as to help them reduce the difficulty of operation, improve work efficiency, and ensure product quality.
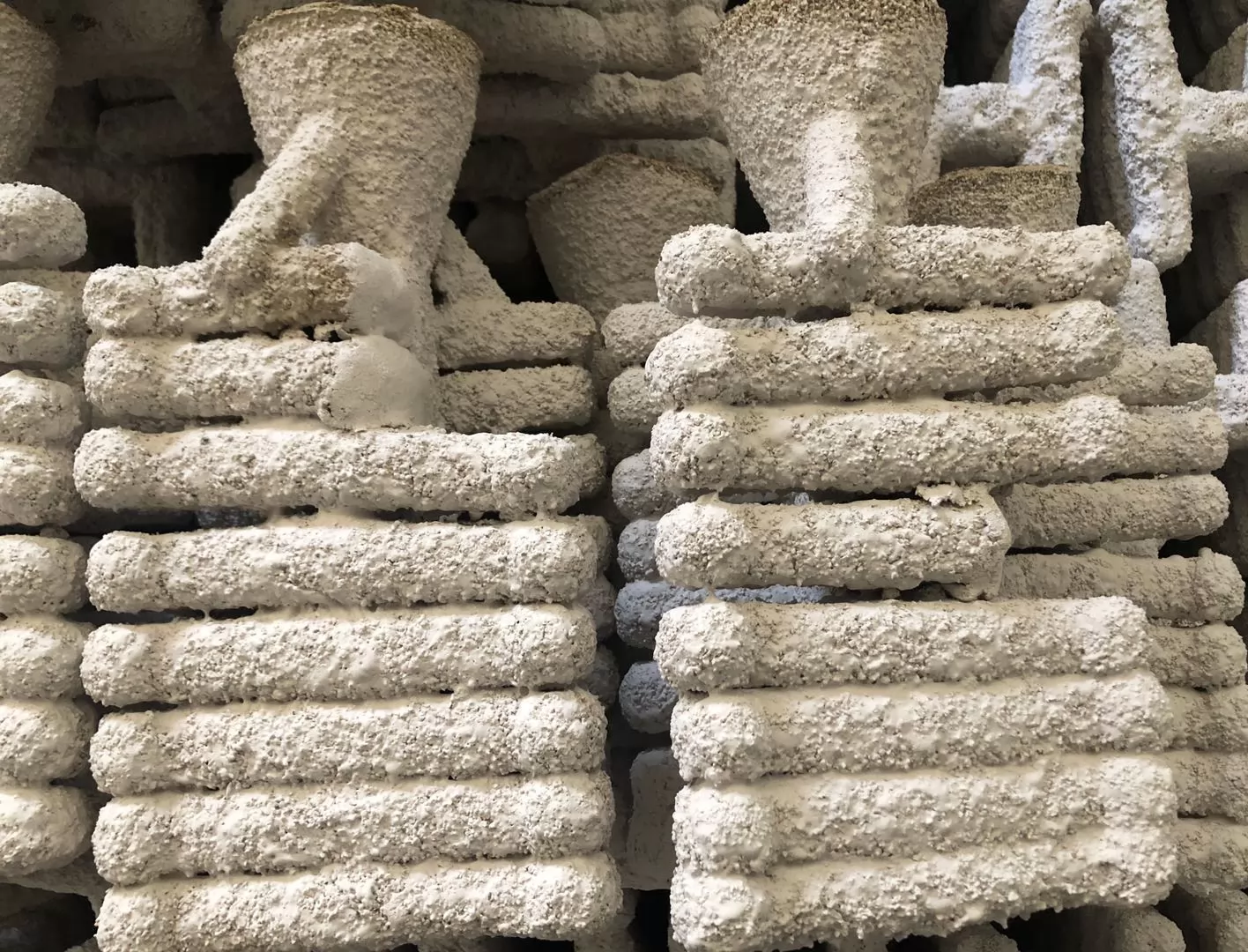
The last thing to talk about is casting. Cast iron is mainly manifested as molten steel. The reason is that the mold shell is cracked. Improper dewaxing operation and collision during handling will cause the mold shell to crack before casting. Therefore, it is also necessary to strengthen the skill training of the dewaxing workers, and the furnace workers to inspect the mold shells before firing. If there are broken parts and cracks, they should be repaired in time. In addition, the molten steel is too heavy, and the mold shell cannot bear the weight, which will cause cracks. This involves the improvement of the welding process.
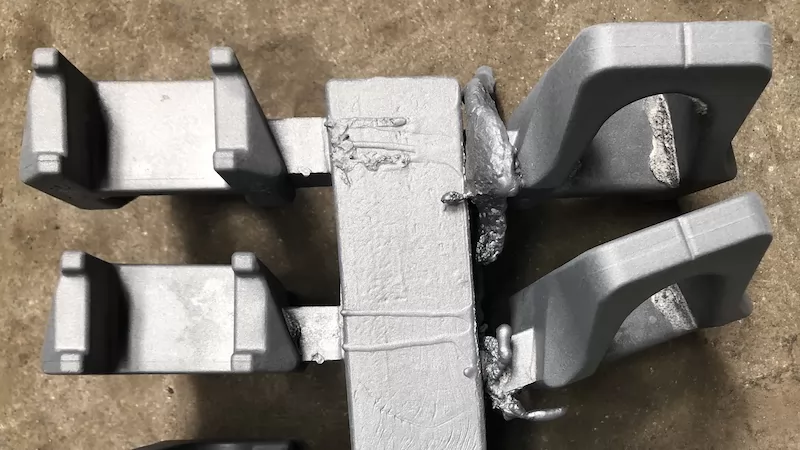
In summary, the defects of iron clamping in castings are mainly found in welding, shell making, and casting. As long as these three are controlled, most of the iron clamping problems can be solved. Thank you for reading this article. If it helps you, it will be an honor. You are welcome to contact Besser Casting by any means.